Счастливая десятка
Железо - величайшее открытие, сделанное человеком; открытие его существования, его необычайных свойств (мягкое в чистом виде, сверхпрочное в сплавах), способов получения разнообразных сталей. Железо - главное измерение современной цивилизации. Вот какой наш XX век - железный! Как он начался несколько тысячелетий тому назад, так и продолжается до сих пор.
Первые куски железа, которыми воспользовались наши предки, как считают ученые, упали с неба в виде железных метеоритов и, обработанные, служили прежде всего оружием. Да и в средние века тоже. Нельзя удержаться, чтобы не привести отрывок из романа Вальтера Скотта «Ричард Львиное Сердце». «Костюм всадника. Кольчуга с длинными рукавами, стальные перчатки и стальные латы считались, по-видимому, еще недостаточно надежным прикрытием, ибо на шее всадника висел еще треугольный щит, а стальной шлем с капюшоном был снабжен воротником из стальных колец, прикрывавшим плечи и горло воина и заполнявшим отверстие между латами и головным убором. Его икры и, колени, как и все тело, были защищены кольчугой, а ноги обуты в стальные башмаки, сделанные из таких же стальных пластинок, как и перчатки...»
Да, многовато приходилось стали на душу одного рыцаря. И все же общее производство ее в те времена было ничтожно мало. Впрочем, больше, чем на оружие да невольничьи цепи, его и не требовалось. Прошли века, и с каждым столетием железо завоевывало для себя новые жизненные пространства.
Железо - главная забота страны. Возьмите статистические отчеты о выполнении государственных планов. На первом месте стоят данные о выплавке чугуна и стали. В 1928 году началась первая пятилетка. И началась она со строительства новых металлургических заводов. Через тридцать лет мы с гордостью говорили: выплавка стали за эти годы увеличилась почти в тринадцать раз.
Идет десятая пятилетка. А производство стали продолжает оставаться в центре внимания партии и правительства. Но теперь уже «обеспечить в 1980 году производство стали в количестве 160-170 млн. тонн и готового проката-115-120 млн. тонн» А как это выполнить? Ответ также содержится в «Основных направлениях развития народного хозяйства СССР на 1976-1980 годы»: «Осуществлять техническое перевооружение отрасли, модернизацию действующих и ввод в эксплуатацию новых мощных металлургических агрегатов. Совершенствовать и шире внедрять прогрессивные способы производства и улучшения качества металла: выплавку стали в кислородных конверторах...» В конверторах получают так называемые «рядовые» стали. Однако «рядовые» ни в коей мере не означает второ- или третьесортные, а скорее наиболее требуемые промышленности и строительству, и должны они обладать строго определенными качествами. До восьмидесяти процентов рядовых сталей дают конверторы. И наряду с мартенами способствуют развитию нашего «железного века».
В. Маяковский предсказывал: «Я знаю - город будет, я знаю - саду цвесть, когда такие люди в стране советской есть». Эти слова горят по вечерам на привокзальной площади Новокузнецка. От нее прямыми лучами устремляются широкие улицы, пересекаемые проспектами и бульварами. Новокузнецк - город своеобразный, расположен между сопками, и потому районы его довольно далеки друг от друга. Весной склоны сопок зацветают белой кипенью яблонь, груш, вишен, деревья на улицах и бульварах, в скверах выбрасывают зеленые, остро пахнущие свежестью листья - и как будто не было долгой и суровой зимы с короткими днями и пронзительными морозами.
Есть город. Есть сад. И как продолжение их - фантастическая графика нового металлургического завода. Собственно, это даже не завод, а скорее комбинат, состоящий из ряда производств, но называется «Запсиб-метзавод». Он логическое продолжение знаменитого КМК - Кузнецкого металлургического комбината - детища первой пятилетки. Главный инженер Кузнецк-строя академик И. Бардин, чьим именем названа одна из главных улиц Новокузнецка, в своей книге «Жизнь инженера» вспоминает: «Котлован первой домны начали копать в апреле 1930 года. Землю рвали динамитом. Она взлетала черными фонтанами и медленно, точно нехотя, опускалась. Взрывы сотрясали воздух. Лопались стекла в окнах только что отстроенных зданий заводоуправления и базисного склада. Мы делали котлован глУбиной в пять-шесть метров. Работу гнали в три смены. Работали и ночью, при электрическом свете нашей первой трехкиловаттной станции. Механик нашел эту динамомашину (так тогда называли электрогенераторы) на мельнице в старом Кузнецке. Динамо питало двадцать лампочек...»
Так это начиналось.
Продолжение не только в новых домнах и мартенах, в современных прокатных станах, в совершенном оборудовании, продолжение - в людях, в наших современниках, без которых ничего бы этого и не было. На «Запсибе» есть ККЦ-2 - второй кислородно-конверторный цех. Это действительно новое и уникальное прея приятие черной металлургии...
Но прежде несколько слов о самом конверторе и конверторном производстве стали.
Конвертор - это печь, но очень своеобразная: этакий наигромаднейший сосуд из стали, выложенный изнутри толстым жаростойким слоем из огнеупорного кирпича и напоминающий по форме кринку с сильно раздутыми, боками. В конвертор под стать ему ковшом выливают расплавленный чугун, совком величиной с железнодорожную платформу засыпают металлолом, добавляю десятка полтора-два тонн извести, другие компоненты подводят фурму - трубу и через нее подают под давлением кислород, то есть ведут так называемую продувку. Расплавленная масса бурно закипает, начинается варка стали, иными словами, железо освобождается от лишнего углерода и примесей.
Из-под металлической юбки, которой прикрыта горлЯ вина конвертора, вырываются раскаленные газы и веера искр. Но самое потрясающее и захватывающее зред лище предстает перед глазами, когда конвертор наклоняют для взятия пробы и можно заглянуть (разумеется, сквозь стекла специальных очков, а то и ослепнут недолго) внутрь котла. Кратер действующего вулкана! Расплавленный металл бурлит, выбрасывая из середины на поверхность огненные фонтаны. Темно-малиновые пузырищи с треском лопаются, оставляя после себя круги с рваными краями. Нестерпимый красный свет заливает цех. Ощущается жар приблизившегося солнца даже за толстым стеклом дистрибуторной - довольно просторной комнаты, вознесенной на двадцать пять метров от пола цеха, где установлены различные приборы и откуда оператор конвертора или дистрибуторщии управляет плавкой. Дистрибуция - распределение. Дистрибуторщик и впрямь распределяет: когда и сколько нести шлакообразующих элементов (известь, плавиковый шпат), агломерата (обогащенная железная руда для охлаждения), как низко опустить фурму, сколько времени вести продувку...
Проба показала - сталь готова. Ее сливают в ковш. Весь процесс конверторной плавки длится 30-40 минут.
Идея такого способа варки стали: чугун + лом+ продувка = сталь - остается прежней с момента его изобретения. Однако, чтобы получить больше стали, изменяется конструкция конверторов, их объем, интенсивность продувки, то есть время плавки. Вот в первом цехе «Запсиба» работают конверторы объемом сто тонн каждый, а во втором -триста пятьдесят тонн. За сутки один конвертор может дать более двух десятков плавок (при всем при том, что и на подготовку требуется довольно много времени) или сварить 8000 - 10 000 тонн стали.
Это о конверторе. А человек? Может ли он справиться с таким объемом и такой скоростью продувки, даже если речь идет о стотонных конверторах? Вот тут-то и начинаются трудности. Дистрибуторщик знает, сколько залито в конвертор чугуна и какой он температуры, сколько засыпано лома и других компонентов, но он лишь приблизительно представляет, как проходит варка стали. Дело в том, что во время продувки па плавку действует масса, как говорят специалисты, неконтролируемых возмущений, то есть факторы, которые влияют на процесс приготовления стали, но измерить которые, чтобы вмещаться, невозможно. Скажем, металлический лом. Обыкновенный, школьники насобирали отходы производства. Нет такого прибора, чтобы определить, сколько в нем консервных банок, которые легко плавятся и мало влияют на снижение температуры плавки, и сколько слитков, которые значительно охлаждают сталь. И еще: грязный лом или чистый? Не станут же загрязненный отмывать синтетическим стиральным порошком. Но если и станут, возникнет еще вопрос: насколько хорошо прополоскали «выстиранный» металлолом? Ведь остатки порошка тоже будут влиять на качество стали.
Очень много факторов действует на температуру варева в конверторе. А как ее замерить? Термометр не поставишь - он сгорит, расплавится в доли секунды. Есть, правда, такие температурные датчики, которые за кратчайшее время жизни в расплавленном металле успевают послать человеку информацию. Но их нужно много, они дороги, и потому использовать их крайне невыгодно.
А самое главное, как узнать химический состав стали в любой момент продувки? Поступают так. Продувку останавливают, конвертор наклоняют, берут пробу, отправляют ее в химическую лабораторию. На это уходит драгоценное время.
И все же сталь в конверторах варят, много и хорошего качества. Как же все-таки оператор конвертора управляет плавкой? Что ему помогает? Во-первых, знания. Недаром же дистрибуторщики - люди со средним, специальным и даже высшим образованием. Во-вторых, опыт. Необходимую информацию о процессе он получает по косвенным данным: по характеру и обилию искр, вылетающих из конвертора, по цвету расплавленной стали, по температуре отходящих газов и так далее, а также по химанализу после первой повалки (остановка продувки для взятия пробы). Так было.
Но вот появляются вместо стотонных трехсотпятиде-сятитонные конверторы, продувка сокращается с 20-25 до 10-15 минут, новые конструкции конверторов лишают возможности получения некоторых данных по косвенным признакам (горловина, через которую можно было заглянуть в конвертор, закрывается «юбкой»). И если раньше в шести случаях из десяти дистрибуторщик в чем-то все-таки ошибался и сталь приходилось «доваривать», тратя лишние минуты, то теперь человек просто не в состоянии за такой короткий срок переработать обилие информации (больше - приблизительной, меньше - точной) и принять единственно правильное peшение.
Однако то, что не может сделать человек, может машина. Когда таскать тяжести стало невмоготу, он изобрел колесо и соорудил повозку, в которую запряг лошадь. Сейчас в «повозки» запрягаются десятки и сотни лошадиных сил. И в деле с конверторами со всей очея видностью встала проблема создания машины, которая бы если и не полностью, то хотя бы частично заменила дистрибуторщика или, по крайней мере, стала бы его добрым и объективным советчиком. Этакий многознающий быстромыслящий робот-консультант.
Новый конверторный цех, о котором уже упоминалось, начал строиться на «Запсибе» в 1972 году, тогда же и начало рождаться «существо», появившееся на свет спустя несколько лет под труднопроизносимым именем ИАСУТПиП ККЦ-2 ЗСМЗ: интегрированная автоматизированная система управления технологическим процессом и производством кислородно-конверторного цеха-2 Запсибметзавода. Это и есть робот, который консультирует человека, советует ему, ведет с ним диалог, резюмирует беседу и принимает решение. Оператору конвертора остается согласиться с этим решением или внести в него какие-то коррективы. А в конце плавки будет видно, кто оказался прав: машина или человек. Робот с дотошностью опытного бухгалтера записывает весь процесс плавки, свой диспут с человеком и какие принимались решения. (Эти записи, как выяснится позже, имеют огромное, если не первостепенное значение).
За разработку и внедрение ИАСУТПиП ККЦ-2 «Запсиба» десять молодых ученых, инженеров, математиков, металлургов удостоены премии Ленинского комсомола в области науки и техники 1977 года. Вот имена лауреатов: Александр Кошелев, Сергей Карепов, Михаил Петрунин, Александр Кропочев, Владимир Отц, Леонид Мышляев, Борис Сидоренко, Петр Пигида, Валентина Баранчук, Игорь Виноградов.
Они закончили разные институты, у них разные характеры, разные личные друзья. Но судьба собрала их в одном городе (только Игорь Виноградов из Москвы); научный и производственный интерес вовлек в одну работу и сплотил в единый (хотя они из двух организаций) творческий коллектив, которому и удалось решить сложнейшую проблему - создать АСУ конверторного Цеха. Систему достаточно уникальную, представляющую собой шаг вперед в теории и практике автоматизированных систем управления технологическим процессом.
...Когда наступает весна, томительное беспокойство подкрадывается к Леониду Мышляеву. Он гонит его: некогда - работы много. Но вот приходит лето, снег давно стаял, реки вошли в свои берега и гонят воды по гористой Туве, перекатываясь через пороги и срываясь водопадами. Дух странствий охватывает Леонида, и он уже ничего с собой не может поделать: начинает готовить снаряжение, чтобы отправиться в путешествие на плотах по непокорным рекам Тувы. Этот удивительный край еще сохранил свою природу почти нетронутой. Там леса не вырублены, и рыба не пугана, и медведицу с медвежатами можно встретить. А бурная вода доставляет немало острых ощущений плывущим на плотах, воздвигая преграды за преградами: пороги, крутящиеся воронки, водопады и стремительное течение в русле, узко зажатом между скалами. Это неутомимо быстрое движение с постоянным преодолением и любит Леонид. Здесь среди дикой природы и в единоборстве с ней глубже постигаешь суть бытия и назначения человека.
К глубине постижения через преодоление Леонид стремится чуть ли не со школьной скамьи. Закончив в городе Белове восьмилетку, он поступил в Прокопьевский горный техникум на автомобильное отделение и закончил его с отличием. И сразу подал документы в Новокузнецке в Сибирский металлургический институт (СМИ): автомобили, которые он изучил достаточно хорошо, казались ему уже слишком простыми, тянуло к познанию более сложных вещей, хотелось, как говорит Мышляев, «поковыряться на уровне абстрактных понятий, копать глубже, где непонятно, где преграды. Меня всегда привлекал не сам род деятельности, а ее глубина».
В институте Леонид познакомился и подружился с Михаилом Петруниным и с Александром Кошелсвым. Они слушали одних преподавателей, особенно восхищаясь Виталием Павловичем Авдеевым, доцентом кафедры автоматизации металлургических процессов. Впоследствии В. Авдеев окажет им большую помощь в работе над АСУ. Заниматься у него было чрезвычайно интересно. Он никогда не читал лекций в полном смысле слова «читать», а беседовал со студентами, вовлекая их в обсуждение проблемы на равных.
Все трое занимались в студенческом научном обществе, проводили исследования на кафедрах с огромной заинтересованностью, со страстью. Времени ие хватало. Приходилось распределять его по всем делам с точностью до минут. Книги читали только самые важныбИ Каждый выбирал для себя свои. Мышляев предпочитал да и до сих пор предпочитает Шекспира: «Какие страсти! Какая целеустремленность! Дела людей до предела ла спрессованы во времени. А теперь на что мы порой тратим не минуты - часы? Шекспировские страсти. Не даром мы так говорим. А бесстрастный человек убежден, ничего сделать не сможет. Ни в жизни, ни в искусстве, ни тем более в пауке или технике». Михаил Петрунин: «Люблю Чехова - коротко и впечатлительно».
Отправляясь в путешествие по рекам Бурятии, Мышяев не раз брал с собой Петрунина. Кошелев, провожая их, напутствовал: «Смотрите головы там себе не Ломайте, они еще нужны человечеству». А сам шел домой и принимался за очередную главу диссертации «О программно-статическом управлении конверторной плавкой стали».
Валентина Баранчук тоже из СМИ. Окончила школу в деревне Луговое и поступила в Омский пединститут на биологический факультет. Но после первого же семестра поняла: биология не ее дело. Влекло к точным наукам. «К математике, - говорит Валентина, - я всегда хорошо относилась. И она ко мне тоже. У нас с ней взаимная любовь. Вот я и ушла из биологов». Год она работала санитаркой в больнице. А потом приехала в Новокузнецк. Ее приняли в СМИ на специальность инженера-металлурга цветных металлов.
Получила Валентина диплом и отправилась по распределению в Улан-Удэ. Но работа не очень нравилась: однообразная и совсем не по специальности. Вернулась в Новокузнецк. Как раз в это время московский Центральный научно-исследовательский институт комплексной автоматизации (ЦНИИКА), создавший проект АСУ конверторного цеха-2, организовал там свой сектор. Валентина Баранчук и поступила туда младшим научным сотрудником, точнее, программистом вычислительных машин. И сразу же ей вплотную пришлось заняться АСУ ККЦ-2. Сразу - это почти через год, так как прежде всего необходимо было учиться и переучиваться, вначале в Кемерове, потом полгода в Северодонецке. И не столько там, на специальных курсах, сколько самостоятельно. Валентина приближалась к АСУ.
Сергей Карепов и Владимир Отц учились в Томске. Сергей -в университете на факультете прикладной математики, Владимир - в политехническом по специальности физика твердого тела.
Получив диплом, Сергей стал работать в Сибирском физико-техническом институте в Томске, в лаборатории счетно-решающих устройств отдела кибернетики. Он занимался вопросами математической логики. И, пожалуй, с самого начала был ближе других к работе над автоматизированной системой управления.
Владимир начал свою карьеру специалиста по АСУ в Новокузнецком секторе ЦНИИКА. Потом перешел на завод и опять переквалифицировался - стал электронщиком, освоил вычислительную машину М-6000. Отличный инженер, верный товарищ, остроумный собеседник. Хорошо играл на гитаре, пел. Даже скучную и неинтересную работу мог оживить какой-нибудь смешной проблемой. В бюро до сих пор вспоминают, как на уборке картошки целый день все веселились, разрабатывая поставленный Отцем вопрос: как можно было бы механизировать труд, если бы картофель рос клубнями вверх. Владимир очень любил природу, часто ходил на охоту. Там и произошла эта случайная нелепая трагедия. Он так и не узнал, что стал лауреатом. Товарищи, друзья Отца тяжело переживали утрату, такую неожиданную и такую горькую.
Александр Кропочев и Петр Пигида - бывшие педагоги. Александр окончил физмат Новокузнецкого пединститута и работает сейчас в запсибовском бюро программирования отдела вычислительной техники. Петр - выпускник физмата Абаканского пединститута. Он попал в ту же лабораторию, что и Валентина Баранчук, под начало Бориса Сидоренко, блестящего инженера, по словам главного конструктора АСУ конверторного цеха заведующего лабораторией ЦНИИКА А. Белостоцкого, «он всегда полон творческих идей и замыслов».
В разработке и внедрении АСУ ККЦ-2 участвовали две организации: Запсибметзавод и ЦНИИКА. Они были, так сказать, генеральные ее создатели. Однако еще добрый десяток институтов и предприятий имели к ней непосредственное отношение: те, кто обеспечивал АСУ вычислительной техникой, приборами, другой аппаратурой. Координация их действий, осуществление связей с разработчиками и исследователями, решение различных организационных вопросов было поручено Игорю Виноградову. Он же участвовал и в разработке технического задания на программирование АСУ.
Игорь служил в знаменитой Таманской дивизий, учился в Москве в институте стали и сплавов. Шахматист-перворазрядник. Работа программистом помогает ему лучше играть в шахматы, а шахматы, упорядочивая мышление, работать над автоматизированными системами управления.
Разными путями пришли лауреаты премии Ленинского комсомола к созданию АСУ, но очень много в них общего: берутся за самое трудное, стремятся познать непознанное, не боятся овладевать новыми и новыми профессиями, чтобы из бесконечного их множества найти свою единственную...
Перед создателями АСУ ККЦ-2 стоял прежде всего вопрос: что, собственно, надо улучшать в управлении конверторной плавкой. Можно автоматизировать управление всего процесса, а можно оптимизировать лишь управление продувкой. Первый путь хотя и более желательный, но несравненно более сложный, трудоемкий, дорогостоящий, нежели второй путь. Поэтому выбрали продувку.
А как решить? У любой задачи есть несколько решений. У этой тоже. Либо АСУ - советчик дистрибутор-щика, либо АСУ работает в режиме обучаемого человеко-машинного взаимодействия, то есть диалога между человеком и машиной на уровне принимаемых решений. Машина беседует с дистрибуторщиком об управлении основным процессом плавки в трехсотпятидесятитонном конверторе, о продувке. Образование, знание и опыт позволяют человеку вести такой диалог. А машина? На что она будет опираться? Чему ее научить? Какие вложить знания? Какой передать опыт? Абсолютно все она не воспримет - не «резиновая». Значит, машина должна действовать по строгой программе, оперируя в определенной последовательности информацией, получаемой от датчиков, производить необходимые расчеты (это не займет много времени, так как применяемые УВМ М-6000 выполняют 200 тысяч операцией в секунду) и лишь после этого что-либо советовать человеку или принимать какие-то решения. Словом, требовалось разработать алгоритм АСУ. Этим и занимались бюро Александра Кошелева и группа Бориса Сидоренко, параллельно и взаимосвязанно.
Но чтобы яснее представить, что же все-таки они сделали, немного вообще об алгоритме.
Автоинструктор начинающему водителю: включите зажигание, проверьте, не стоит ли машина на скорости, включите стартер, одновременно нажимая слегка на акселератор, дайте двигателю немного поработать, чтобы он согрелся, контролируя температуру по прибору, отожмите сцепление, включите первую скорость, прибавьте обороты, плавно опустите сцепление, увеличьте скорость, внимательно следя за дорогой, чтобы не наскочить на фонарный столб, отожмите сцепление... Ну и т. д. Если перепутать перечисленный порядок манипуляций, автомобиль не заведется или не тронется с места, а то, чего доброго, и испортится. Инструктор выдал алгоритм пуска двигателя автомобиля и начала его движения. Любой алгоритм и есть четко предписанная последовательность действий, выполнение которой гарантирует достижение цели.
Давайте проследим одну линию, которая вкупе с другими привела к основной принципиальной идее создания алгоритма управления конверторной плавкой в АСУ ККЦ ЗСМЗ.
Михаил Петрунин тогда еще работал инженером-исследователем в центральной заводской лаборатории. Он выявлял оптимальный состав лома для конверторной плавки: сколько его надо и какого качества. Первоначально задумывали найти оптимальный состав для всех плавок. Но так как они, плавки, резко отличаются друг от друга, то этот оптимум не давал правильного решения. Тогда встала проблема определения состава лома для каждой плавки в отдельности. И этого решить не удалось. Михаил обратился за советом к Леониду Мышляеву. Прообсуждав несколько вечеров, решили показать свои наметки В. Авдееву. К нему же за советом пришел и Александр Кошелев. Тут же вчетвером и взялись за петрунинскую проблему.
В результате той беседы на кафедре автоматизации металлургических процессов СМИ родился предварительный вариант алгоритма назначения массы лома для конверторов - росток идеи для создания алгоритма управления конверторной плавкой на основе реставрации хороших управлений прошедшими плавками с последующим прогнозированием на предстоящую плавку.
Можно предположить, что так и работали древние металлурги. Они не владели теорией металлургических процессов, химических превращений, высоких температур, не знали кристаллографии и многого другого, чем сейчас вооружены ученые и практики. Но металл-то был нужен. И в больших количествах. И хорошего качества. А у древних металлургов под руками не было ничего, кроме опыта предшествующих плавок. Они опирались на него и только на него. И создавали то, что мы бы сейчас назвали алгоритмом управления плавкой, с помощью его прогнозировали предстоящие плавки и получали дамасскую сталь.
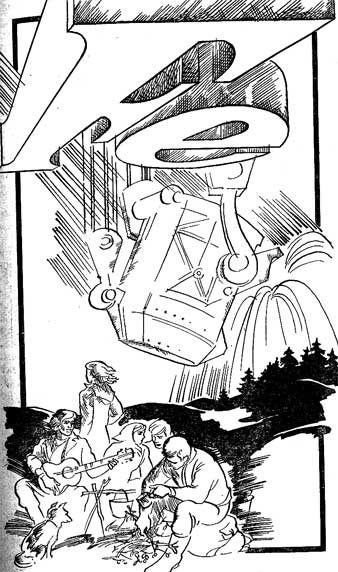
Счастливая десятка
Идея оглядываться на предыдущий опыт проста, да собственно, так и поступает оператор конвертора. Управляя продувкой. Но ведь речь-то идет о том, чтобы эту работу выполняла машина при отсутствии точной информации о плавке. Возникает вопрос: а можно ли, анализируя прошедшие плавки, управлять предстоящей? Вначале этот вопрос был решен на качественном уровне, то есть машина могла (пока теоретически) ответить на: что? в каком порядке? Но возникало: сколько? Тут приходилось разводить руками. И чтобы руки, а вслед за ними и машина вывели рекомендующую цифру, разработчикам АСУ пришлось обратиться к методам современных математических теорий, оперирующим вщ роятностными понятиями: теория вероятностей и математическая статистика, теория автоматического управления и теория игр, которая занимается определением стратегии играющих сторон.
Нельзя сказать, что молодые создатели АСУ работали на голом месте. Нет. В то время как сибирский Гипромез (Государственный институт по проектированию металлургических заводов) проектировал второй кислородно-конверторный цех, ЦНИИКА разрабатывал АСУ этого цеха, хотя ни его самого, ни какого-то прообраза и подобия в мире не существовало. И ясно, что с проектом цеха появился лишь проект АСУ, точнее даже сказать, некая приближенная ее модель. Как, предположим, определить усвоение извести по ходу продувки? Проект алгоритма утверждал: анализируя изменение шлака. А каким образом получить такой анализ - неизвестно (уже говорилось, что датчики в печь не ввести). Знать же, как известь усваивается, очень важно: ведь она - ложка, которой вычерпываются вредные для стали фосфор и сера. Ничтожные примеси фосфора - и сталь «хладнолом», так называют металлурги, когда резко увеличивается ее хрупкость. Серы больше допустимого-«краснолом»: сталь не выдерживает высоких температур.
Модернизацией, изменением (порой коренным), приспособлением таких функциональных алгоритмов к производственным условиям как раз и занималась группа Александра Кошелева.
И алгоритм управления конверторной плавкой постепенно приобретал стройность, логическую завершенность. Но работал он пока на бумаге. Брали предполагаемые данные, которыми будет оперировать алгоритм, и засылали их в него, а он выдавал решения: как управлять плавкой в тех или иных ситуациях. Эти управленческие решения показывали технологам, главным специалистам для оценки. И те, анализируя, говорили: тут не пойдет, там не получится. И часть элементов разработки начинали с нуля. Вновь расчеты, проверки и перепроверки. И как тут молодым инженерам помогала их дружба! Леонид Мышляев говорит: «Наша дружба с Петруниным и Кошелевым скреплена общими интересами, общей работой». Сколько вечеров они просидели вместе, обсуждая результаты исследований, находя совместными усилиями наиболее точные ответы на вопросы, сыпавшиеся как из рога изобилия. Каждый правильный ответ - кирпичик в алгоритм управления плавкой.
А Бор.ис Сидоренко, Петр Пигида и Валентина Бараичук связывали функциональные алгоритмы с единым алгоритмом системы и разрабатывали алгоритм информационной части АСУ. Они работали с ЭВМ. Но при всем при том возможности электронно-вычислительной машины ограничены. Поэтому нужно выбирать рациональную, как называют специалисты, конфигурацию технических средств для ЭВМ - для ее «ушей» и «глаз».
Чтобы судить о температуре автомобильного двигателя, датчики можно поставить в воду, которой он охлаждается, в камеру сгорания цилиндров, в выхлопные трубы, в картер. Анализируя данные приборов, можно составить достаточно полное представление о температурном режиме двигателя. Но способен ли водитель на мгновенный анализ такого количества данных. Нет, разумеется. Конструкторы нашли выход: ставят только один датчик и один прибор. Еще ни один шофер не пожаловался на нехватку информации о температуре двигателя.
Поиском подобных выходов из обилия положений, но на Уровне ЭВМ и занималась группа Бориса Сидоренко. Сергей же Карепов и Александр Кропочев переводят алгоритм с логико-математического языка на язык УВМ. 1-10 это была далеко не «техническая», даже на самом высоком ровне, работа. Машина хоть и «умная», да е же «ограниченная»: и объем ее памяти относительно невелик, и «соображает» не так уж быстро - «всего» 200 тысяч операций в секунду. Потому и получалось: здесь недостанет ей быстродействия, тут не хватит памяти. Вот и приходилось идти программистам на упрощения, но чтобы не в ущерб содержанию. Так часто посту, па ют переводчики, однако разговаривающие на разных языках стороны отлично понимают друг друга.
Владимир Отц осуществлял привязку алгоритма к УВМ М-6000 и позволил тем самым реализовать алгоритм АСУ.
Прошло несколько лет, и оправдались надежды А. Кугушина (Александр Андреевич, кандидат технических наук, депутат Верховного Совета РСФСР, делегат XXV съезда КПСС, директор «Запсиба», был тогда главным инженером завода), начальника отдела вычислительной техники В. Соловьева, Ю. Борисова - бывшего начальника конверторного цеха, а ныне начальника производственного отдела завода, которые поверили в молодые силы и доверили разработку и внедрение ИАСУТПиП ККЦ-2 инженерам, лишь недавно закончившим институты. Система работает и дает огромный экономический эффект. Одна из первых в стране. И тут важно отметить, что АСУ ККЦ-2 управляет не только собственно технологическим процессом выплавки стали, но и дает руководству цеха, диспетчерам, экономической службе, операторам конверторов оперативную п объективную информацию о ходе производства.
В дистрибуторной - мнемосхема, на которой отражается весь процесс плавки стали в конверторах (такая, же схема есть и в диспетчерской, и на рабочей площадке у конверторов); дисплей - станция индикации данных (СИД), - похожий на обыкновенный телевизор, только не с голубым, а с зеленым экраном; телетайп, связанный с ЭВМ, за которым сидит оператор электронно-вычислительной машины. На экране СИДа возникают цифры: данные загрузки конвертора и управляющие рекомендации. Дистрибуторщик оценивает их и сообщает оператору ЭВМ то, в чем он не согласен с машиной. Оператор передает ей мнение человека. Та «отвечает»... Идет диалог между человеком и машиной. Наконец вырабатывается совместное решение. На все это уходят считанные секунды. Во время продувки дистрибуторщик следит за тем, что еще скажет машина, какие внесет изменения в управление плавкой. Соглашается ей или нет: последнее слово остается за человеком - с приводит в движение управляющие рычаги, кнопки, тумблеры.
Плавка окончена. Готовая сталь слита в ковш. Лаборатория провела химический анализ. Весь процесс варки -тали описан и зафиксирован в специальной документации. Теперь можно сравнить управленческие решения человека и машины. Лучшие войдут в «банк» будущих управлений. Накопленную информацию машина использует также для составления и печати большого количества отчетных документов о работе цеха. Они позволяют анализировать экономические показатели деятельности не только цеха в целом, но и каждой бригады, каждого сталевара: кто даже при одинаковом количестве полученной стали меньше израсходовал сырья и материалов, более рационально использовал оборудование, получил металл лучшего качества.
И именно потому, что АСУТПиП ККЦ-2 ЗСМЗ управляет выплавкой стали, обеспечивает информацией работников цеха, проводит экономический анализ, в начале названия этой системы и появилась буква «И» - интегрированная: ИАСУТПиП - интегрированная автоматизированная система управления технологическим процессом и производством.
Такова АСУ конверторного цеха-2: одна из составных общей АСУ «Запсиба», которую разрабатывают совместно ЦНИИКА и завод. «Эта система, - говорит главный конструктор АСУ ЗСМЗ кандидат технических наук А. Белостоцкий, - включит ряд АСУ технологическими процессами на основе идей АСУ второго конверторного цеха, будет управлять основными производствами завода и координировать их работу между собой. И называться она будет ОТАСУ ЗСМЗ - организационно-технологическая автоматизированная система управления Запсибметзавода». И, возможно, к тому времени отпадет надобность и в человеке-операторе. «Наша мечта - сказал В. Соловьев, - сделать замкнутый процесс Управления выплавкой стали, в том числе и другие стадии, такие, как раскисление, легирование плавки в ковше без участия человека». «При полной автоматизации,- продолжает его мысль Л. Мышляев, - человек передвинется на другую, более интеллектуальную работу. Интеллектуализация человека и есть, возможно, главная подоплека процесса полной автоматизации».