2. РАЗВИТИЕ МЕТАЛЛУРГИИ
Изменения в технике черной и цветной металлургии
Создание машиностроения и других отраслей крупной индустрии потребовало технического перевооружения металлургии. Значение металлов и сплавов быстро возрастало, что вызвало необходимость увеличить выплавку чугуна, железа, стали и специальных сплавов на основе железа, а также цветных металлов (меди, олова, цинка и их сплавов, некоторых редких металлов). Известные ранее способы получения железа, применявшиеся в мануфактуре, уже не могли удовлетворить требований производства пи в количественном, ни в качественном отношении.
Возросший спрос на железо привел к крупным изменениям в доменном производстве. Развитие черной металлургии базировалось главным образом на двустадпйном производстве железа: выплавке в доменной печи чугуна, с последующим переделом его в железо в кричном горне. Усовершенствованная доменная печь, оборудованная соответствующими техническими устройствами, была рассчитана на непрерывность действия; в то же время передел чугуна в железо был процессом периодическим. Выплавленный в доменной печи чугун был жидким, а крица в кричном горне - пористой, тестообразной, твердое железо в ней было перемешано с жидким шлаком.
Со второй половины XVIII и до 70-х годов XIX в. в доменном деле произошли крупнейшие технические сдвиги: возросли высота и объем доменных печей, улучшился коэффициент использования их полезного объема, интенсифицировался сам процесс. Этому способствовали перевод домен на горячее дутье воздухом, нагреваемым в специальных аппаратах - кауперах, переход на минеральное топливо, использование новых средств подачи воздуха в печь.
Доменные печи мануфактурного периода работали исключительно на древесном угле, потребность в котором возрастала соответственно увеличению темпов производства металла. Это привело к уничтожению лесов на огромных территориях ряда западноевропейских стран. Особенно тяжелый топливный кризис ощущали Англия, Франция и другие страны с высокоразвитой черной металлургией. Острая необходимость в металле и отсутствие лесов побудили, например, английских предпринимателей ввозить металл из других стран, в том числе из России, которая до начала XIX в. играла важнейшую роль в экспорте металла. В 1800 г. Россия производила 10 млн. пудов чугуна, в то время как Англия - всего лишь 8 млн. пудов.
Идея замены древесного угля в доменном процессе другим видом топлива высказывалась в Англии еще в XVII в. Однако попытки использовать минеральное топливо в металлургическом производстве долгие годы не давали положительных результатов, так как в то время еще не были изучены физико-химические процессы, происходящие в печи, и условия коксования каменного угля.
В 1619 г. (по другим сведениям - в 1621 г.) [1, с. 9] англичанин Дод Додлей взял патент па производство чугуна, применив для этого каменный уголь. При этом изобретатель получил чугун хорошего качества [2, с. 12]. Несмотря на прогрессивность предложения Д. Додлея, ему пришлось вести ожесточенную борьбу с предпринимателями, изготовлявшими чугун на древесном угле. В результате Д. Додлей разорился и прекратил свои работы по усовершенствованию выплавки чугуна.
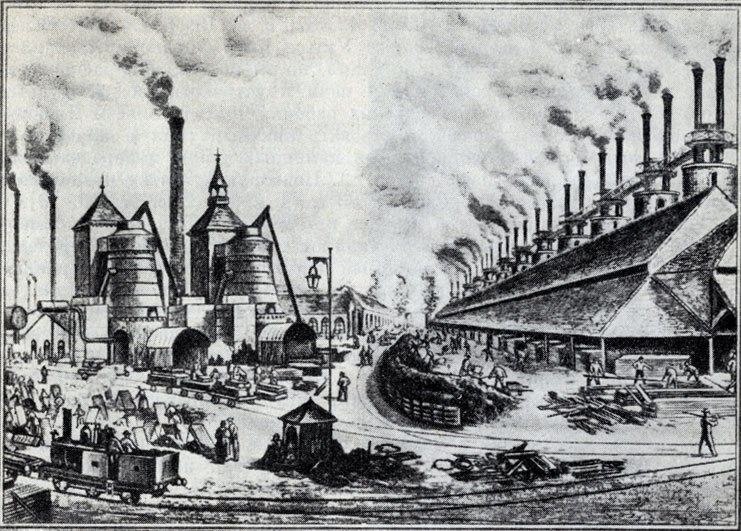
Общий вид металлургического завода с доменной печью 60-х годов XIX в. г. Маршен, Бельгия
Практически проблему использования минерального топлива в доменном производстве осуществил в 1735 г. английский инженер-металлург, владелец железоделательного завода в Колбрукдейле Авраам Дерби-сын. Он использовал опыт своих предшественников, но применил для доменной плавки не обычный каменный уголь, а специально переработанный продукт - кокс. Осуществить на практике идею плавки в доменной печи на минеральном топливе было труднее, чем думал Дерби, поэтому ему пришлось изучать физико-химические и технологические факторы, влиявшие на процесс получения кокса. Он испытывал различные новые марки углей, изменял температуру, режимы коксования, подбирал подходящие флюсы для ошлакования примесей. Разрешить проблему доменной плавки удалось лишь после того, как Дерби перешел от применения каменного угля, содержащего большое количество золы и других примесей, преимущественно серы, к использованию кокса. Нововведение, предложенное Дерби, ряд лет не выходило за рамки его собственного производства. Только с 1747 г. кокс стали применять на других металлургических заводах Англии. Результаты не замедлили сказаться: к 1796 г. в Англии плавка чугуна на древесном угле была прекращена и 121 доменная печь, работающая на коксе, выплавляла около 7750 тыс. пудов чугуна [3].
Применение более калорийного кокса потребовало увеличения количества подаваемого в доменную печь воздуха. На своем заводе Дерби применил для привода воздуходувок паровую машину Ныюкомеиа. Она приводила в действие насосы, которые подавали уже ранее отработанную воду на водяные колеса - двигатели воздуходувных мехов. Несмотря на то, что сам паровой двигатель не обладал универсальностью и был маломощным, но даже и этот небольшой дополнительный приток воды на колеса позволял увеличить количество воздуха, подаваемого в домну.
В России первые попытки применить каменный уголь в качестве минерального топлива для доменного процесса были предприняты в 1795 г. на Луганском чугунолитейном заводе Донбасса [4]. Организация выплавки чугуна на минеральном топливе была начата в 1845 г. в Керчи, где была построена доменная печь, предназначенная для работы на антраците. Продолжались и другие опыты, которые в 1870 г. закончились весьма успешно на Лисичанском казенном заводе. Доменная печь этого завода, работавшая на минеральном топливе, выдала в первый год 200 т, во второй 510 т чугуна [5, с. 142].
Доменное производство совершенствовалось по мере интенсификации металлургического процесса. Продолжала улучшаться система подачи воздуха в домну, росла мощность двигателей, приводивших в движение воздуходувные устройства. Клинчатые меха стали заменять цилиндрическими, а позже - центробежными воздуходувками. Применение воздуходувных машин в доменном производстве Англии началось с 1782 г. Однако более прогрессивные центробежные воздуходувки получили распространение с 50-х годов XIX в., что разрешило проблему подачи необходимого количества воздуха в домну.
Утилизацию отходящих газов с целью экономии топлива начали использовать еще в конце XVIII - начале XIX в. Так, в России с 1805 г. на Кусинском заводе на колошнике доменной печи была сооружена рудообжиговая печь, работавшая на колошниковых газах. В 1807 г. подобные печи для обжига руды действовали на Златоустовском и Саткин-ском заводах. В 1819 г. эти печи еще работали на Златоустовском заводе, о чем свидетельствуют описания и зарисовки устройств, сделанные П. П. Аносовым [6]. За рубежом известны результаты опытов французского заводчика Оберто. В 1809 г. он начал эксперименты использования колошниковых газов для цементации железа, обжига кирпича и пр. В 1811 г. Оберто получил привилегию на эти способы [2, с. 23; 7, с. 156].
Доменный воздухонагреватель впервые был применен Дж. Нилсоном на шотландском заводе Клайд. Патент на это изобретение он получил в 1828 г. Нагрев подаваемого в печь воздуха до 150-300° С позволил снизить расходы топлива до 40% и таким образом резко повысить производительность доменных печей. В России опыты использования подогретого дутья для доменных печей, работающих на минеральном топливе, осуществили в 1829 г. на Александровском литейном заводе в Петербурге. Аналогичные опыты были повторены в 1835 г. на Петрозаводском железоделательном заводе, где благодаря использованию подогрева дутья возросла выплавка чугуна и сократился расход топлива.
Горячее дутье применяли в опытном порядке также на Выксунском (1837 г.) и Верх-Исетском уральских заводах. Около 1867 г. оно было введено на двух домнах Билимбаевского завода. В 1870 г. на горячем дутье работала Натальевская доменная печь КУБИНСКОГО завода (Пермская губерния),. Однако широко практически использовать горячее дутье в отечественном доменном производстве стали в 70-х годах XIX в. В 1876 г. на металлургических заводах России действовало около 20 воздухонагревательных устройств [5, с. 132; 8, с. 363-364; 9; 10].
Рост эффективности и повышение производительности отмечается после изобретения специального аппарата для подогрева воздуха, подаваемого в домну в результате утилизации тепла отходящих газов. В 1857 г. англичанин Э. Каупер предложил использовать тепло отходящих газов доменной печи для подогрева специального воздухонагревательного устройства - каупера. Использование кауперов сыграло огромную роль в развитии доменного производства. Оно повлекло важные изменения в конструкции доменных печей и технологии доменного процесса: увеличились размеры и возросла производительность домен.
Широкую известность в черной металлургии получили многофурменные доменные печи (до 10 фурм) с шахтой эллиптического сечения без распара с постепенным расширением к колошнику. Изобретателем этого типа печей был русский горный инженер В. К. Рагдет, получивший на свое изобретение привилегию 22 февраля 1862 г. Рашетовские доменные печи отличались выгодным распределением дутья, что позволило увеличить шахту печи и обеспечить более низкую стоимость выплавляемого чугуна. Печи В. К. Рашета были построены в начале 70-х годов XIX в. на ряде Уральских и других заводов. В г. Нижняя Салда работала многофурменная доменная печь Рашета высотой 50 футов (20 м). Стоимость 1 пуда чугуна, получаемого в домнах Рашета, была почти на 8% ниже стоимости чугуна, выплавляемого в обычных доменных печах [11, 12].
Прогресс в области доменного производства наглядно иллюстрируется ростом емкости доменных печей. Так, объем доменных печей, едва достигавший в начале XIX в. 50 м3, увеличился к 1864 г. до 450 м3, а в 1870 г. превысил 1160 м3. Выплавка чугуна резко повысилась. Например, Англия, выплавлявшая в 1780 г. 40 тыс. т чугуна, довела его выпуск в 1856 г. уже до 3,5 млн. т, т. е. за 76 лет выплавка чугуна возросла в этой стране в 87,5 раза.
В конце XIX в. металлургические заводы Юга России были оснащены крупными доменными печами. Так, например, на Александровском заводе Брянского общества в Екатеринославе (ныне г. Днепродзержинск) работали домны, суточная выплавка которых составляла до 9-10 тыс. пудов чугуна [13].
Характерной особенностью развития металлургии был переход от кричного процесса передела чугуна в железо - к пудлингованию.
Процесс пудлингования возник как крупное техническое новшество в 60-х годах XVIII в. При создании конструкций пудлинговых печей был использован опыт применения в XVII в. пламенно-отражательных печей, которые использовались для производства литых изделий из бронзы. В таких печах во Франции, России и других странах плавили металл для отливки колоколов и статуй [14]. В XVIII в. подобные печи применяли в Швеции и Англии для плавки чугуна.
История знает смелые попытки использовать для передела чугуна отражательные печи. Очень близко к этой мысли подходил Ф. Блюстон, который предлагал в 1677 г. переделывать чугун на каменном угле в пламенной печи, переконструированной из кричного горна. Основатель Карронских железоделательных заводов Джон Робук получил патент (25 октября 1762 г.) на процесс, близкий к пудлингованию, но не смог реализовать свое изобретение [1, с. 12, 87; 2, с. 15; 7, с. 115]. Вслед за ними заводской мастер в Южном Уэльсе Петр Оньонс предложил в 1783 г. вариант процесса пудлингования, но он не получил распространения из-за сложности конструкции печи и устройства воздуходувных мехов. В 1766 г. двое колбрукдельских рабочих братья Томас и Джордж Кранедж предложили переконструировать кричный горн в пламенную печь: эту печь они нагревали, сжигая каменный уголь, и переделывали в ней чугун на железо (патент 1766 г.). Подобную попытку предпринял также Джон Кокшет в Америке в 1783 г. [1, с. 87; 2, с. 37; 15; 16].
Братья Кранедж разделили рабочее и топочное пространство пламенной печи, стремясь изолировать металл от топлива во время передела. Обе части печи имели так называемый пламенный порог, предохраняющий расположенный в ванне металл от непосредственного контакта с топливом. В результате во время плавки значительно уменьшилось количество серы, переходящей из топлива в металл; появилась возможность достичь более спокойного и равномерного шлакообразования по сравнению с кричным горном. Для лучшего соприкосновения металла со шлаком металл непрерывно перемешивали, откуда и произошло название этого процесса - пудлингование, т. е. перемешивание.
Были и другие попытки создать новый способ передела чугуна в железо. Однако наибольшую известность получило изобретение Генри Корта, который при пудлинговании использовал уже получившие распространение обыкновенные отражательные печи и разработал все четыре операции пудлингования (патент 1784 г.).
Подробное описание патента, опубликованное Д. Перси [2], дает представление о существе процесса, предложенного Г. Кортом. Оно сводится к следующему. Чугун в чушках (с железными шлаками или без них, с окалиной и железными обрезками) загружали в нагретую до высокой температуры отражательную («воздушную») печь и нагревали до расплавления. Затем металл перемешивали до тех пор, пока он не начинал переходить в тестообразное состояние и свариваться. В этот момент добавляли окалину, излом или обрезки («обсечки») железа. Полученное железо накатывали в крицы. Крицы, нагретые «до бела, до вара», проковывали под молотом и разбивали на полукрицы. Дальнейшая обработка заключалась в нагревании полукриц и прокатке их в «плющильных» валках, имевших несколько ручьев. Но, кроме того, Г. Корт предлагал вместо чушкового чугуна заливать в отражательную печь жидкий чугун, а полученные крицы железа обрабатывать всеми известными до того способами: в кричном горне, в тиглях и т. д.
В этом же патенте Г. Корт рекомендовал использовать при различных способах получения железа и стали прокатные валки с ручьями его конструкции, что способствовало уплотнению и выдавливанию из металла шлаков (патент на процесс прокатки в калиброванных валках получен изобретателем в 1783 г.) [7, с. 116-117]. Изобретатель использовал валки для получения из криц полосового железа. Применение прокатных валков в схеме пудлингования Г. Корта было наиболее оригинальной особенностью его изобретения. Оно чрезвычайно сокращало трудную операцию обработки крицы под молотом и давало возможность проводить работу быстро, получая большое количество железа в виде различных полос и профилей. Весь процесс получения крицы продолжался около 2-3 ч. Изобретение Г. Корта быстро распространилось во многих странах.
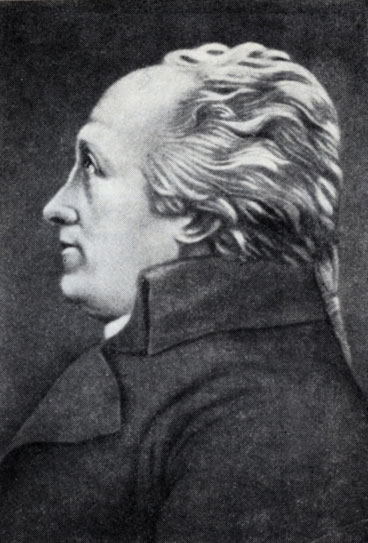
Генри Корт (1740-1800 гг.)
Общее устройство пудлинговой печи конца XVIII в. для пудлингования каменном угле состояло в следующем. В топке сжигается топливо. Продукты горения через пламенный порог попадают в рабочее пространство печи, где на поду находится загруженный чугун с железистыми шлаками. Шлаки под действием пламени переходят в тестообразное состояние и частично расплавляются. С повышением температуры чугун начинает плавиться, и примеси его выгорают за счет кислорода, заключенного в шлаках. Таким образом, чугун обезуглероживается, т. е. превращается в крицу губчатого железа. В рассматриваемой печи предусмотрены две трубы, из которых одна находится над топкой, а вторая расположена в конце печи. Дополнительный дымоход над топкой открывается в тот момент, когда требуется снизить температуру ванны, после чего происходит тщательное перемешивание металла и шлаков.
В России первые опыты по переделу чугуна в железо в пудлинговых печах были осуществлены еще в 1817 г. на Пожевском заводе. В пудлинговой печи на песчаной подине было переработано несколько пудов чугуна. Топливом служили дрова, поэтому пудлингование, рассчитанное на каменный уголь, пришлось приспосабливать к дровам. Так как на Урале имелись большие лесные массивы, полностью обеспечивавшие в то время производство железа в кричных горнах, способ пудлингования распространялся на железоделательных заводах России медленно и еще в конце 30-40-х годов применялся в единичных случаях. Опыты пудлингования проводились в 1836 г. на Боткинском (Камско-Боткинском) заводе, где было создано много вариантов пудлинговых печей. К 1843 г. пудлинговое производство Боткинского завода включало следующее оборудование: «...8 пудлинговых печей, 5 сварочных или проварочных, 1 обжимного лобового молота для проковки пудлинговых криц, 1 хвостового молота для проковки проварочного железа, 3 прокатных станов в шести парах валков и одного о трех, который приспособлен собственно для выделки мелкосортного железа, 1 резного стана, пяти дровосушильных печей и машины для пиловки и колотья дров» [17]. Вслед за Боткинским заводом в России были сооружены пудлинговые печи на Чермозском, Выксунском, Вильском, Унженском, Велетминском и других заводах. Производство пудлингового железа в России достигло в 1866 ir. 12537 тыс. пудов; кроме того, в это время в кричных горнах выделывалось до 5774 тыс. пудов кричного сварочного железа [7, с. 17].
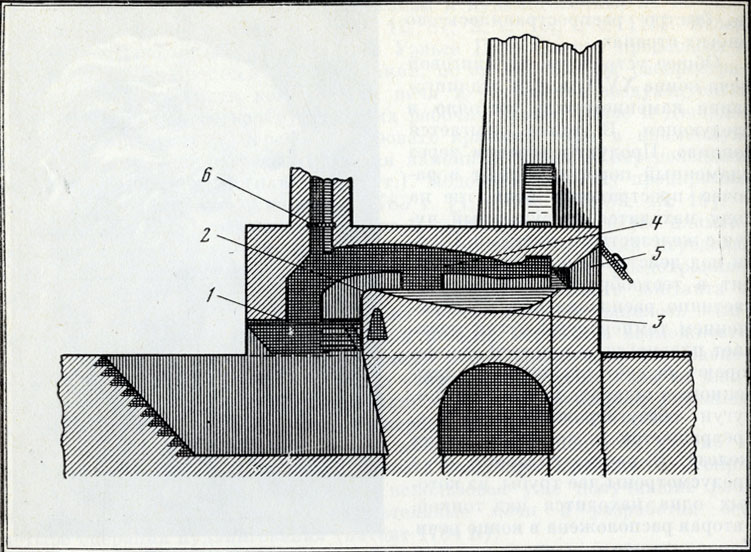
Пудлинговая печь конца XVIII в. для пудлингования на каменном угле 1 - топка; 2 - пламенный порог; 3 - под печи; 4 - рабочее пространство печи; 5 и 6 - трубы
Наряду с производством сварочного железа (кричного и пудлингового) в рассматриваемый период развивался тигельный способ получения литой стали. Идея и первые опыты получения однородной литой стали путем растворения железа в расплавленном чугуне принадлежат известному французскому ученому P. А. Реомюру [18].
Однако наибольшую известность получили работы Б. Гентсмана (Англия), осуществившего в 30-х годах XVIII в. ряд успешных попыток добиться однородной стали расплавлением в тигле стали, полученной цементованием. Из этой стали Б. Гентсман изготовлял часовые пружины. В 1740 г. недалеко от Шеффильда он пустил сталелитейный завод для производства различных изделий и инструмента из тигельной стали [19].
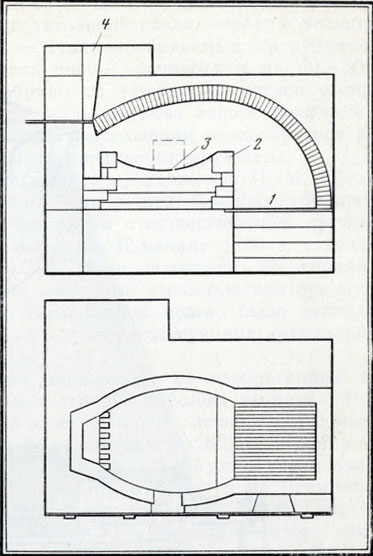
Устройство пудлинговой печи Пожевского завода (Урал), отапливаемой дровами (1817 г.) 1 - топка; 2 - пламенный порог; 3 - под рабочего пространства печи; 4 - дымоход
Тигельную сталь весьма широко применяли в машиностроении в XIX в. На заводе Крупна в Эссене (Германия) в 1811 г. начали отливать пушки из тигельной стали, получаемой по способу Б. Гентсмана. Однако процесс выплавки тигельной стали продолжал совершенствоваться в разных странах вплоть до 50-60-х годов XIX в.
Большую роль сыграли работы русских металлургов Боткинского завода (1809 г.) и С.-Петербургского завода хирургических инструментов (1808г.).
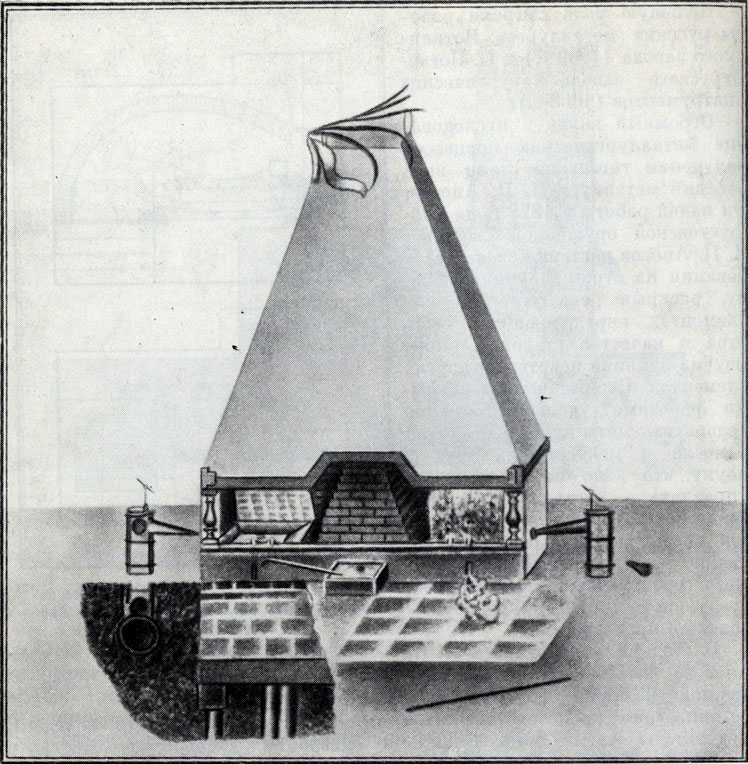
Кричный горн (1830 г.)
Огромный вклад в исследование металлургических процессов получения тигельной стали внес русский металлург П. П. Аносов. Он начал работы в 1828 г. на Златоустовской оружейной фабрике. П. П. Аносов поставил свои исследования на строго научную основу, раскрыв роль углерода как элемента, определяющего свойства и качество сталей, а также изучил влияние некоторых других элементов. Своими замечательными работами ученый стремился превратить металлургию стали из ремесла и искусства в точную науку, что дало бы возможность управлять металлургическими процессами. В результате П. П. Аносов создал четыре основных варианта технологии получения лучшего сорта углеродистой стали - булата, которые легли в основу заводского производства.
Благодаря деятельности П. П. Аносова на Златоустовской оружейной фабрике (Урал) было организовано производство литой тигельной стали высокого качества. Результаты своих многолетних исследований ученый опубликовал в «Горном журнале» в статьях: «О приготовлении литой стали» (1837 г.), «О булатах» (1841 г.), «Описание нового способа закалки стали в сгущенном воздухе» (1827 г.) и ряде других. Начав исследования по получению тигельной стали, П. П. Аносов обратил особое внимание на обеспечение сталелитейного производства высококачественными отечественными тиглями - массивными сосудами из огнеупорной глины, которые могли выдерживать температуры, превышающие температуру плавления стали. Осуществив серию блестяще задуманных и прекрасно выполненных экспериментов по сплавлению железа, чугуна и различных добавок - флюсов, ученый сделал крупный шаг вперед в разработке технологии получения высококачественной стали и изделий из нее. П. П. Аносов впервые раскрыл тайну получения булатной стали, из которой в древности отковывали чудесные стальные сабли и клинки с узорами. Клинки и сабли из булатной стали П. П. Аносова отличались красотой и изяществом, по орнаменту и механическим свойствам их трудно было отличить от тех, которые изготовляли много веков тому назад на древнем Востоке искусные мастера [20-22].
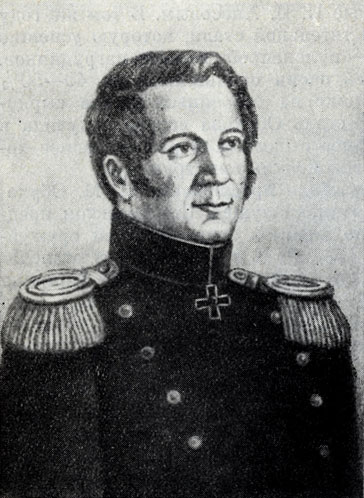
Павел Петрович Аносов (1799-1851 гг.)
Тигельная сталь сыграла огромную роль в развитии высококачественной артиллерии. Когда в 50-х годах XIX в. в военном деле появились нарезные орудия, для их изготовления потребовалась высокосортная однородная по составу сталь, которую можно было получить в значительных объемах, только используя известный тогда тигельный процесс. В этом производстве крупных успехов добились заводы Крупна державшие, однако, в строжайшем секрете способы отливки однородных по составу стальных заготовок для орудийных стволов.
В России проблему получения крупных и однородных стальных отливок для пушек успешно разрешил горный инженер П. М Обухов на Златоустовской оружейной фабрике. В 1854 г. его назначили управляющим этого предприятия. В то время здесь еще работали опытные мастера и сохранились традиции, заложенные П. П. Аносовым. В том же году П. М. Обухов получил первые плавки тигельной стали, которую успешно применили для изготовления кирас - пуленепробиваемых нагрудников. Кирасы из тигельной стали оказались очень прочными и на 40-50% легче кирас, производившихся на фабрике из сваренных листов сырцовой стали и железа. Литая тигельная сталь Обухова вскоре получила в России широкое распространение. Из нее выделывали разнообразное холодное оружие, ружейные стволы и высокопрочные инструменты.
В 1857 г. Военное ведомство рассмотрело предложение П. М. Обухова об использовании литой стали для отливки пушек. Его проектом предусматривалось сооружение в Златоусте рядом с существующей оружейной фабрикой новой сталелитейной фабрики. К началу 1860 г. сталелитейная фабрика была построена. Она была оснащена 96 горнами, в каждый из которых помещалось по два тигля емкостью полтора пуда стали. При одновременном действии всех горнов можно было отливать стальные заготовки весом почти 300 пудов, соответствующих артиллерийскому стволу 24-фунтовой пушки [23].
В 1857 г. П. М. Обухов получил привилегию на изобретенный им способ получения однородной тигельной стали в крупных отливках. Русская обуховская сталь не уступала по качеству крупповской и английской стали и была гораздо дешевле. На состоявшейся в 1862 г. Всемирной промышленной выставке в Лондоне сталь и пушки Обухова были очень высоко оценены. Одна из пушек Обухова, представленная на Всемирной выставке, выдержала без разрушений и изменений более 4 тыс. выстрелов, за что получила золотую медаль. П. М. Обухов организовал в Петербурге орудийный завод, считавшийся одним из передовых в техническом отношении предприятий мира.
Бурное развитие железнодорожного строительства, завершение перехода морского транспорта от деревянных парусных судов к металлическим, возросший спрос на железо и сталь военной промышленности и машиностроения стимулировали расширение производства железа и стали, выдвинули повышенные требования к качеству металла.
Однако существовавшие в то время два вида производства сварочного железа (кричный и пудлинговый) и тигельный способ получения литой стали уже не могли отвечать возросшим требованиям тяжелой промышленности. Производство сварочного железа в кричных и пудлинговых лечах отличалось продолжительностью процесса и трудоемкостью. Что же касается тигельного способа получения стали, то он был дорогим и имел весьма ограниченное применение. Назрела необходимость в коренных изменениях железо- и сталеделательного производств.
Проблема массового получения литой стали разрешена в 1856 г. английским изобретателем Г. Бессемером, который предложит передел жидкого чугуна в литую сталь с помощью продувания через него воздуха в конверторе. Чугун превращается в сталь в результате окисления содержащихся в нем кремния, марганца и углерода. При этом выделяется значительное количество тепла, достаточное для поддержания металла в жидком состоянии. Процесс бессемерования отличается высокой производительностью: для переработки в конверторе 10 т чугуна требовалось не более 10-20 мин, в то время как для передела такого же количества чугуна в кричном горне затрачивалось 3 недели, а в пудлинговой печи 3 дня [13]. Однако, несмотря на явные преимущества этого процесса, по сравнению с традиционными способами производства сварочного железа его широкое распространение в металлургической промышленности развитых капиталистических стран началось лишь с 70-х годов XIX в. Внедрение бессемеровского способа получения литой стали тормозилось, во-первых, необходимостью его технического усовершенствования; во-вторых, недостаточным спросом на литой металл, и, в-третьих, необходимостью крупных капиталовложений, на что капиталистические фирмы, уже вложив большие средства в пудлинговые производства, шли неохотно [24]. Кроме того, внедрение бессемеровского процесса тормозилось охранным патентом, выданным Г.. Бессемеру. Потребовалось около 20 лет упорного труда металлургов, инженеров и ученых, чтобы бессемеровский процесс стал широко распространенным.
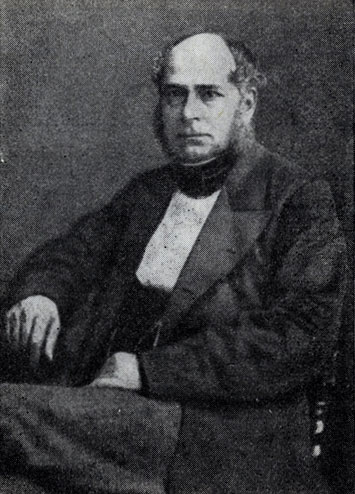
Генри Бессемер (1813-1898 гг.)
Вытеснение пудлингового металла литой сталью привело к образованию на металлургических заводах крупных неиспользуемых запасов пудлингового железа, в результате чего выявилась потребность его переработки в сталь.
Эту задачу удалось успешно разрешить в 1864 г. французскому металлургу П. Мартену, предложившему новый способ получения стали в регенеративных пламенных печах. П. Мартен использовал разработанный незадолго до этого (1856 г.) немецким инженером Ф. Сименсом принцип регенерации тепла продуктов горения, применив его для подогрева воздуха и газа. В результате изобретателю удалось получить в печи температуру, достаточную для выплавки стали. В мартеновской печи плавка чугуна и лома (скрапа) сопровождается химическим взаимодействием металла, шлака и газа. Первая регенеративная пламенная печь, построенная П. Мартеном во Франции (1864 г.), имела емкость 1,5 т. В 1870 г. мартеновское производство было введено в России после создания инженером А. А. Износковым первой мартеновской печи (с загрузкой 2,5 т) на Сормовском заводе. Мартеновское производство развивалось весьма интенсивно, увеличивалась емкость печей и возрастала выплавка мартеновской стали.
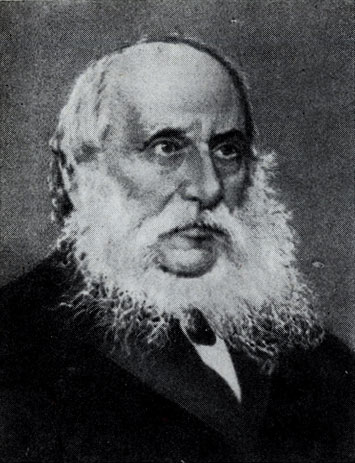
Пьер Мартен (1824-1915 гг.)
К числу крупнейших достижений в области металлургии 70-х годов XIX в. необходимо отнести также создание так называемого томасовского способа получения литой стали, позволившего перерабатывать жидкий фосфористый чугун. Процесс был разработан в 1878 г. английским металлургом С. Томасом.
Создание и развитие новых способов получения литой стали (бессемеровский, мартеновский и томасовский) были в рассматриваемый период крупнейшим техническим достижением, революционизировавшим несколько позже железо- и сталеделательное производство.
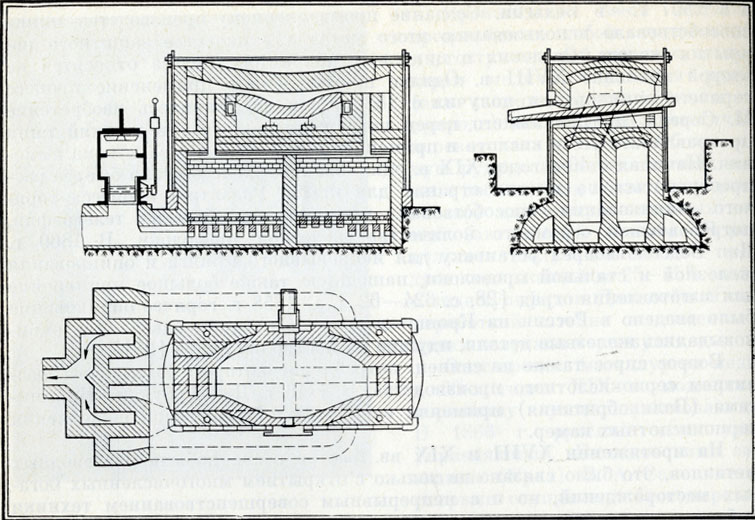
Печь Мартена в Сирейле (Франция) для плавки литой стали
В разработку научных основ металлургии железа и стали большой вклад внесли русские ученые. Особого внимания заслуживают работы А. С. Лаврова и Н. В. Калакуцкого, открывших в 1866 г. явление ликвации в стали и установивших зависимость ликвации от размеров слитка. В результате были объяснены процессы кристаллизации и внутренних напряжений в слитках и намечены пути к повышению качества отливок. В 1868 г. Д. К. Чернов открыл фазовые превращения в стали при ее нагревании, установив критические точки, т. е. температуры, при которых в стали происходят полиморфные превращения, определяющие ее структуру и свойства. Это открытие и последующие работы Д. К. Чернова заложили основы современного металловедения и термической обработки стали [25].
Развитие капиталистического производства глубоко затронуло и цветную металлургию. Прогресс машиностроения, паровой энергетики, транспорта, приборостроения, развитие химической, текстильной, бумажной промышленности, военной и других областей техники резко повысили спрос на цветные металлы. Возникла необходимость в техническом перевооружении металлургических предприятий, строительстве новых заводов, разработке и практическом использовании новых методов выплавки и обработки металлов и сплавов с целью получения необходимых конструкционных материалов и изделий из них.
В развитии цветной металлургии рассматриваемого периода необходимо отметить две характерные особенности: первая - непрерывный рост выплавки и совершенствование способов производства ранее известных цветных и благородных металлов (меди, олова, свинца, цинка, ртути, сурьмы, золота, серебра), вторая - открытие и разработка методов получения новых металлов.
Производство меди (второго после железа металла), ранее широко используемой в виде сплавов с оловом (бронзы) в декоративно-художественных работах и для отливки пушек и колоколов, ко второй половине XVIII в. и особенно после промышленной революции конца XVIII - начала XIX в. стало заметно расти в связи с применением меди в новых отраслях техники. Мировая выплавка меди, составлявшая в 1800 г. 20 тыс. т, возросла к концу XIX в. до 500 тыс. т [26, с. 41].
Производство меди издавна представляло собой трудоемкий многоступенчатый процесс, в котором медные сернистые руды (они широко распространены в природе) после обжига частично переводились в окиси. Обожженную руду плавили в шахтных печах с добавлением кокса (немецкий способ) или в отражательных печах (английский способ). В результате получался штейн - продукт, содержащий до 25-45% меди в виде сульфидов. Дальнейшей переработкой штейна в пламенных печах получали черновую медь.
Этот процесс металлургии меди в 60-х годах XIX в. подвергся коренному усовершенствованию. В 1866 г. русский металлург, управляющий Богословскими заводами (Урал) В. А. Семенников впервые осуществил бессемерование медного штейна для передела его в черновую медь. Медный штейн поступал из шахтных печей непосредственно в конвертор с
круглым сечением. Через фурмы пропускали воздух (проводили опыты и с водяным паром), что позволило более чем в 5 раз ускорить процесс передела штейна в черновую медь. В. А. Семенников доказал возможность доведения меди в штейне до 76% [27].
Последователи В. А. Семенникова - русские металлурги А. А. Иосса и Н. В. Лалетин приняли участие в завершении разработки этой технологии. После введения бессемерования процесс выплавки меди стал более простым. Расплавленный в отражательной печи штейн продували в конверторе на белый штейн, содержащий 76-80% меди. Затем в той же отражательной печи расплавляли белый штейн и продували его в конверторе на черновую медь с содержанием до 99% основного металла [5, с. 178].
Возросший спрос на медь и ее сплавы вызвал увеличение производства олова и цинка, входящих в состав бронз и латуней. Кроме того, цинк и олово нашли новые области применения, в частности в технологии горячего покрытия других металлов с целью защиты их от коррозии.
С середины XVII в. в Германии началось промышленное производство белой жести, для чего железные листы погружали в расплавленное олово, в XVIII в. это производство было организовано в Англии и в XIX в. в России [26, с. 117].
Цинк почти до конца XVIII в. был еще большой редкостью в Европе. Правда, в 40-х годах XVIII в. был построен первый цинковый завод в Бристоле (Англия). В 1798 г. началось производство цинка в Силезии, а в 1807 г.- в Бельгии. Создание промышленного производства цинка способствовало использованию этого металла в качестве защитного покрытия железа. Сведения о цинковых покрытиях железа относятся ко второй половине XVIII в. Однако промышленное применение процесс горячего оцинкования получил с 1836 г., когда появилось изобретение М. Сореля, предложившего перед погружением железа в жидкий цинк протравливать его в кислоте и применять в качестве флюса хлорид аммония. Начиная с 40-х годов XIX в. оцинкованное железо стало быстро распространяться во многих странах для крыш. Развитию процесса горячего оцинкования способствовал прогресс в области телеграфии, потребовавшей огромного количества железной проволоки. В 1860 г. Дж. Бедсон изобрел установку для непрерывного отжига и оцинкования железной и стальной проволоки, нашедшую также большое применение для изготовления оград [28, с. 624-625]. С 1858 г. горячее оцинкование 0ыло введено в России на Кронштадтском пароходном заводе, где оцинковывались железные детали, идущие на постройку судов [29].
Возрос спрос также на свинец, потребление которого вызывалось развитием сернокислотного производства. В 1746 г. Дж. Робук из Бирмингама (Великобритания) применял свинцовую обшивку при сооружении сернокислотных камер.
На протяжении XVIII и XIX вв. быстро росла добыча благородных металлов, что было связано не только с открытием многочисленных богатых месторождений, но и с непрерывным совершенствованием техники добычи и извлечения рудного золота.
Ниже приведены данные о ежегодной (в среднем) мировой добыче золота с 1800 по 1870 гг. [26, с. 53]:
Сведения ежегодной мировой добычи золота с 1800 по 1870 гг.
Годы |
т |
1801-1820 |
14,6 |
1821-1840 |
17,2 |
1841-1850 |
54,8 |
1851-1860 |
201,3 |
1861-1870 |
190,3 |
В 1843 г. русский ученый П. Р. Багратион открыл способ извлечения золота из руд с помощью цианистых щелочей, заложив основы современного металлургического процесса - цианирования. Это направление в дальнейшем развили английские металлурги Дж. С. Мак-Артур и братья Р. и В. Форрест (1887-1888 гг.), после чего цианирование прочно вошло в практику мировой золотопромышленности.
С историей благородных металлов связано другое выдающееся научно-техническое достижение первой половины XIX в. - открытие процесса порошковой металлургии (металлокерамики). Зарождение и развитие порошковой металлургии стимулировалось необходимостью получения тугоплавких металлов, выплавка которых обычными методами и в существующих типах плавильных печей не представлялась возможной. Таким металлом, вызвавшим большой интерес, была платина, температура плавления которой составляет 1773° С. Добыча сырой платины в первой половине XIX в. приняла в некоторых странах, в том числе и в России, значительные масштабы. Возникла необходимость очистки сырой платины и технологического ее использования. Вначале для очистки платины ее спекали с белым мышьяком при длительном прокаливании. Это был очень сложный процесс с тяжелыми условиями труда вследствие сильной ядовитости мышьяка.
Впервые чистую ковкую платину и изделия из нее получили методом порошковой металлургии член-корреспондент Российской академии наук П. Г. Соболевский со своим ассистентом В. В. Любарским. О своем замечательном открытии П. Г. Соболевский сделал подробный доклад в Петербурге 27 марта 1827 г. на торжественном собрании Ученого комитета по горной и соляной части. С 12 мая по 1 декабря 1826 г. в лаборатории П. Г. Соболевского было очищено и обращено в ковкое состояние до 97 пудов сырой платины^ а по 1 января 1834 г. - 476 пудов. Методом порошковой металлургии из платины тогда изготовляли монеты, медали, жетоны, полосы, проволоку, чаши, тигли и кружки для питья [30, 31]. Изготовление платиновых изделий методом порошковой металлургии было прекращено после того, как Сент-Клер Девиль (Франция) применил в 1859 г. к платине кислородную сварку водородным пламенем. Однако этот метод был восстановлен в начале XX в. применительно к получению нитей накала из вольфрама и молибдена для электрических ламп накаливания [32].
Качественные сдвиги в металлургии в рассматриваемый период характеризуются открытием и получением в свободном состоянии ^большого числа новых металлов. Достаточно отметить, что за период с 50-х годов XVIII в. до 70-х годов XIX в. усилиями ученых разных стран было получено 28 ранее неизвестных металлов. Среди них цветные, благородные и редкие металлы: никель (1751 г.), марганец (1774 г.), молибден (1781 г.), вольфрам (1783 г.), родий, палладий, осмий, иридий (1803- 1804 гг.), калий (1807 г.), стронций (1807 г.), магний, кальций, барий (1808 г.); кадмий (1817 г.), литий (1818 г.), цирконий (1824 г.), титан (1825 г.), алюминий (1825 г.), иттрий (1828 г.), бериллий (1829 г.), уран (1841 г.), рубидий (1863 г.), индий (1867 г.), ванадий (1869 г.) и др.
Однако большинство открытых и полученных впервые металлов в рассматриваемый период не нашли широкого промышленного использования ввиду их дороговизны, связанной с несовершенством технологии. Области применения некоторых из них ограничивались преимущественно ювелирными работами, изготовлением металлических денежных знаков, медалей и т. п. Так, никель, полученный впервые в свободном состоянии в 1751 г., еще в первой половине XIX в. рассматривался как ювелирный металл, который частично использовали также в сплавах для изготовления монет. С 1850 г. монеты из сплава никеля, меди и цинка стали чеканить в Швейцарии, с 1873 г. - в Германии. К концу XIX в. относится применение никеля в качестве легирующего металла.
Примером длительного освоения некоторых металлов может служить история алюминия. Датский физик Г. X. Эрстед впервые получил его в 1825 г. в ]зиде небольших металлических комочков, восстанавливая хлористый алюминий амальгамой калия.
В 1827 г. немецкий химик Ф. Вёлер извлек небольшие количества порошкообразного алюминия, применив в качестве восстановителя парообразный металлический калий. Работая в области исследования алюминия в общей сложности 17 лет, Ф. Вёлер с достаточной точностью определил основные его свойства, но вплоть до 1845 г. смог получать металл лишь в виде зерен величиной с булавочную головку. Через девять лет, в 1854 г. Сент-Клер Девиль, продолжая работы Ф. Вёлера, разработал способ получения металлического алюминия, положенный в основу первого промышленного его производства. Вместо калия в качестве восстановителя он применил более дешевый натрий, а также установил оптимальные температурные режимы процесса восстановления хлористого алюминия. На Всемирной Парижской выставке 1855 г. алюминий фигурировал уже как промышленный продукт, однако производство его было тогда ничтожно: в 1854-1855 гг. изготовили всего 25 кг алюминия. Тем не менее химический способ Сент-Клер Девиля сыграл большую роль в развитии алюминиевой промышленности. Усовершенствование способа сопровождалось постепенным увеличением производства алюминия, в результате чего его выпуск к 1890 г. достиг около 200 т, одновременно в 20-25 раз была снижена стоимость металла [33].
Освоение производства цветных металлов стало претерпевать быстрые и радикальные изменения лишь в конце XIX в., когда в результате новых успехов химии, физики и металловедения, а также в связи с общим развитием техники и применения дешевой электроэнергии традиционные пирометаллургические способы получения и очистки металлов пополнились принципиально новыми методами. Большую роль в металлургии цветных и редких металлов стали играть электрометаллургические процессы.
В рассматриваемый период были заложены основы таких электрометаллургических процессов, как электролиз водных растворов и электролиз расплавленных солей, обеспечивший прогресс в области открытия и получения в свободном состоянии многих из указанных выше металлов.
В результате совершенствования электролиза уже в первой половине XIX в. появилась новая область прикладной электрохимии - гальванотехника, охватывающая процессы электролитического осаждения металлов на поверхность металлических и неметаллических изделий. В развитии гальванотехники определились два направления: гальваностегия - получение на поверхности изделий прочно сцепленных с ней тонких металлических покрытий и гальванопластика - получение с матриц легко отделяющихся, относительно толстых точных копий с различных предметов.
Открытие и техническая разработка гальванотехники принадлежит русскому ученому Б. С. Якоби, о чем он сделал 5 октября 1838 г. сообщение на заседании Петербургской академии наук. Позже, в 1867 г., за изобретение гальванопластики Б. С. Якоби был удостоен первой премии и большой золотой медали Главным советом Всемирной парижской выставки [34, 35]. Таким образом, с работ Б. С. Якоби начинается развитие электрометаллургической технологии, которая уже в 40-х годах XIX в. получила в ряде стран промышленное развитие.
Наибольших успехов в первый период гальванотехника достигла в технологии электроосаждения на металлические предметы золота и серебра из их растворов. В 1840 г. Д. Р. Элькингтон (Англия) получил привилегию на способ гальванического золочения с применением синеродистых щелочей и хлорного золота [36]. В том же году швейцарский физик Де-ла Рив опубликовал также новый метод покрытия металлических предметов золотом. Д. Р. Элькингтон и Де-ла Рив представили Парижской академии паук шесть рецептов электролитов для золочения, из которых четыре первых содержали синеродистые соединения, пятый - раствор хлористого зОлота и поваренной соли в воде и шестой - раствор сернистого золота в сернистом калии. Заслуга Д. Р. Элькингтона состояла в том, что он добился получения блестящих золотых покрытий, прибавляя к электролиту несколько капель сероуглерода. При этом осадки золота получались не матовыми, а блестящими и более плотными.
В 40-50-годах XIX в. появились работы ряда других ученых по гальванотехнике, способствовавшие дальнейшему распространению технологии электроосаждения благородных и цветных металлов. Процесс электроосаждения стал заметно распространяться с введением электро-машпнных генераторов постоянного тока. В 1842 г. Дж. С. Вульрич получил патент на использование магнитно-электрических машин в технологии электроосаждепия металлов. Первым применил магнитно-электрические машины в промышленном производстве Т. Прайм из Бирмин-гама, использовав патент Дж. С. Вульрича. Однако крупных успехов добился завод Элькингтона в Англии, где была установлена мощная по тому времени магнитно-электрическая машина, позволявшая осаждать 480-560 г серебра в час [28, с. 632-634].
Развитие во второй половине XIX в. гальванотехники оказало огромное влияние на прогресс ювелирного производства. В результате огневые (горячие) методы покрытия благородными металлами в ряде случаев уступили место более экономичным и более совершенным в техническом отношении методам электролитического осаждения. Методы электролитического осаждения постепенно завоевывали все новые области применения. Наряду с использованием золочения н серебрения к 60-70-м годам XIX в. в практику металлургического и металлообрабатывающего производства вошли электролитическое железнение, меднение, никелирование и ряд других процессов.
В 1867 г. на Всемирной парижской выставке русский изобретатель II. М. Федоровский демонстрировал изготовленные им электролитическим путем медные трубки без шва внутренним диаметром от 3 до 240 мм и толщиной стенок от 0,75 до 9,5 мм. И. М. Федоровский сообщил, что разработанным им способом можно осаждать до 100 кг меди. За эти работы он был удостоен серебряной медали [37].
Гальванотехника к концу XIX в. прочно вошла в металлургические процессы, связанные с рафинированием меди, спрос на которую быстро возрастал с развитием электротехнической промышленности. Впервые производство рафинированной меди за рубежом возникло в Германии на заводе «Сименс-Гальске» в 1878 г. Производительность этого завода составляла 500-600 т электролитической меди в год. В России впервые электролитическую медь стали производить в конце 80-х годов XIX в. на Калакентском заводе братьев Сименс (Кавказ). С 1890 (или с 1891 г.) приступил к выпуску электролитической меди завод Николаева в Нижнем Новгороде [36, с. 277-278].
Вторая половина XIX в. ознаменовалась также рядом других открытий в области металлургии, например, изобретением металлотермии, предложенной впервые в 1859 г. русским ученым Н. Н. Бекетовым [38].
Совершенствование технологии обработки металлов давлением
Прогресс в получении металлов и сплавов, особенно в металлургии железа, стимулировал развитие процессов обработки металлов давлением - прокатки, волочения, прессования, ковки и чеканки.
На технику прокатки оказало огромное влияние распространение пудлингования. Лишь после изобретения пудлингования, когда вместо малопроизводительной техники ковки крицы пудлингового железа была введена обработка металлов в калиброванных валках, прокатка как металлургический процесс стала характерной для заводов черной металлургии.
Техника прокатки металлов, в том числе прокатка в калиброванных валках, прошла длительный и сложный путь развития. Ранние сведения о прокатных станках, состоящих из пары валков, приводимых в движение вручную, относятся к XV-XVI вв.
Эволюция прокатного стана с калиброванными валками неразрывно связана с появлением так называемых резательных станков, хорошо известных уже в XVII в. Резательные станки представляли пару валков, снабженных пазами с острыми кромками и применявшимися для получения пруткового железа из листа. В 1728 г. появляются работы Флюера (Франция), прокатывавшего прутки в валках с ручьями (калибрами). Для этого он отковывал заготовки овального профиля, пропускал их попеременно через валки с ромбическими и овальными ручьями и получал прутки диаметром 6,3 мм. Как считают, Флюер был первым, кто понял, что прокатные валки с ручьями овально-ромбической формы наиболее рациональны для обеспечения быстрого обжатия обрабатываемого металла и повышения производительности. Не случайно, что использование овально-ромбических валков легло в основу дальнейшего развития техники сортовой прокатки [39].
На протяжении всего XVIII в. техника прокатки металлов продолжала непрерывно совершенствоваться, в результате прокатные станы все более распространялись в железоделательном производстве. С помощью стальных прокатных валков, приводимых в действие гидравлическими двигателями, изготовляли не только полосовое и шинное железо, но также и железные листы.
Полосы и шины получали в России на прокатных станах, известных под названием плющильных машин. Такие станы, имевшие гладкие валки, были введены на Екатеринбургском заводе (Урал) в 1723 г. В. И. Генниным [40]. Более сложные валки с калиброванными ручьями применяли на уральских заводах еще до 1756 г. [7, с. 113]. К 80-м годам XVIII в. относится начало развития листопрокатного производства в железоделательной промышленности России. До этого времени кровельное железо ковали под молотами. По сути, листопрокатный стан - это та же «плющильная машина», однако у него более тщательно обработаны валки и конструктивно оформлено их строго параллельное положение. Первый листопрокатный стан был установлен в 1782 г. на Чермозском заводе, почти одновременно с появлением станов такого типа в Англии. К концу века такими же листопрокатными станами были оборудованы Сылвенский, Невьянский, Верх-Нейвинский заводы (все на Урале) и Александровский казенный завод. В результате на предприятиях уменьшилось число «дощатых» и «колотушечных» цехов, где кованое железо в горячем состоянии под молотами расплющивалось в листы. Прокатка обеспечивала высокую производительность и качество листов [8, с. 29].
Прокатка как самостоятельный процесс металлургического производства утвердилась к концу XVIII - началу XIX в., что было неразрывно связано с общим развитием машиностроения и использованием для привода прокатных станов паровых двигателей. На протяжении XIX в. появились разнообразные прокатные станы, которые можно подразделить на три основные группы: обжимные, листовые и сортовые. В 30 - 40-е годы XIX в. в промышленно развитых странах начинается прокатка рельсов. В 50-х, годах в Германии появились первые прокатные станы, предназначенные для прокатки крупных балок, бандажных полос для колес железнодорожного транспорт.
В период 40-70-х годов XIX в. были разработаны и получили промышленное использование многие типы современных прокатных станов. В 1856 г. в Швеции О. Е. Карлсунд построил и пустил в г. Мотола первый триопрокатный стаи, позволивший непрерывно пропускать обрабатываемую заготовку в валки без их реверсирования. Правда, идею создания такого стана высказывал ранее известный шведский инженер X. Полем. В Англии триопрокатный стан ввел в 1862 г. на заводе в Бирмингаме бельгийский инженер Б. Лаут. В 1857 г. Дж. Фритц (США) построил мощный трехвалковый стан для прокатки рельсов [28, с. 63, 01; 41, с. 872]. В 1859 г. мастер В. С. Пятов (Россия) построил первый прокатный стан для изготовления корабельной брони [42].
Большим достижением в области прокатки явилось создание и практическое использование в 60-х годах XIX в. непрерывных прокатных станов. Идея непрерывного прокатного стана для производства железных полос впервые была высказана в 1775 г. в России нижнетагильским мастером Е. Г. Кузнецовым. Однако из-за отсутствия в то время достаточно мощных двигателей и необходимых конструкционных материалов осуществить на практике свою идею изобретателю не удалось [43, 44].
Не смог добиться положительных результатов и В. Хезлидайн, получивший в 1798 г. в Англии патент на прокатный стан непрерывного действия [28, с. 63; 45].
Лишь в 60-х годах XIX в. это удалось реализовать английскому механику из Манчестера Дж. Бедсону и Ч. Уайлю. В 1862 г. Дж. Бедсон построил непрерывный проволочно-прокатный стан, отличающийся большой производительностью благодаря автоматической подаче металла от одной пары валков к другой и большой скорости их вращения. Непрерывный стан Бедсона имел 16 пар попеременно расположенных один за другим горизонтальных и вертикальных валков [28, с. 63; 46].
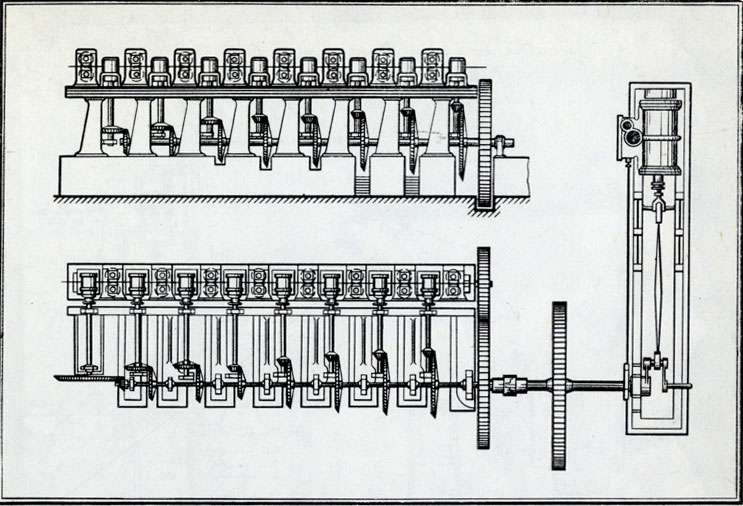
Непрерывный прокатный стан Дж. Бедсона (1862 г.)
Наряду с техникой прокатки весьма интенсивно развивался процесс волочения металлов. До 70-х годов XIX в. проволоку получали на машинах однократного действия, отличающихся низкой скоростью и производительностью. В 1871 г. был запатентован первый непрерывный проволочно-волочильный стан, изобретателями которого были братья Дж. и И. Вуудз (Англия). Непрерывные станы резко повысили скорости волочения, производительность увеличилась в 10 раз [47]. Одну из волочильных машин многократного действия с 14 волоками и полученную на этой машине медную проволоку (диаметром от 0,23 до 0,04 мм) демонстрировали на выставке в Глазго в 1888 г. [28, с. 622].
В первой половине XIX в. начала усиленно развиваться техника волочения труб и крупногабаритных профилей, для чего были сконструированы и получили практическое применение волочильные гидравлические прессы и цепные волочильные станы. Потребность в трубах и полосовых тянутых изделиях стимулировалась быстрым развитием машиностроения и транспорта [47].
Крупные изменения претерпела техника ковки. С развитием прокатных станов, как было показано выше, использование ковки несколько сократилось. Однако процесс ковки продолжал совершенствоваться, находя новые области применения в различных отраслях металлургической и особенно машиностроительной промышленности. На более высокий уровень поднялась практика конструирования кузнечного оборудования, возросли его мощности. Маломощные и тихоходные вододействующие молоты (хвостовой, лобовой и среднебойный) в условиях быстро прогрессировавшего пудлингового производства железа и связанного с ним увеличения веса и размеров поковок для крупногабаритных деталей и частей машин уже не соответствовали возросшим требованиям промышленности. На смену вододействующим пришли паровые молоты, обладающие большой мощностью и производительностью.
В 1784 г. Дж. Уатт, сразу же после получения патента на свой универсальный паровой двигатель, запатентовал и молот с приводом от балансира паровой машины [48, с. 297]. Однако коренной переворот в технике ковки наступил лишь с 1839 г., когда английский изобретатель Дж. Несмит предложил паровой молот, в котором подвижные части с ра-оочим бойком поднимались между двумя направляющими, а для перемещения рабочего органа был использован поршневой цилиндр паровой машины. Молот Несмита выгодно отличался от применявшихся до того рычажных молотов большой высотой подъема бойка и высокой мощностью, позволяющими обрабатывать крупные поковки металла.
В 1842 г. Дж. Несмит получил патент на изобретение, в котором была воплощена идея молота простого действия. В нем сила удара определялась массой падающих частей (поршня, штока и бабы с бойком) и высотой их падения. Вскоре в конструкцию парового молота были внесены существенные усовершенствования: автоматическое парораспределение с помощью специального золотника (1843 г.) и подача пара в верхнюю часть цилиндра. Последнее нововведение положило начало паровым молотам двойного действия: пар не только поднимал рабочий орган молота, но и увеличивал скорость его падения благодаря действию парового давления на поршень в верхней части цилиндра, повышая тем самым силу удара.
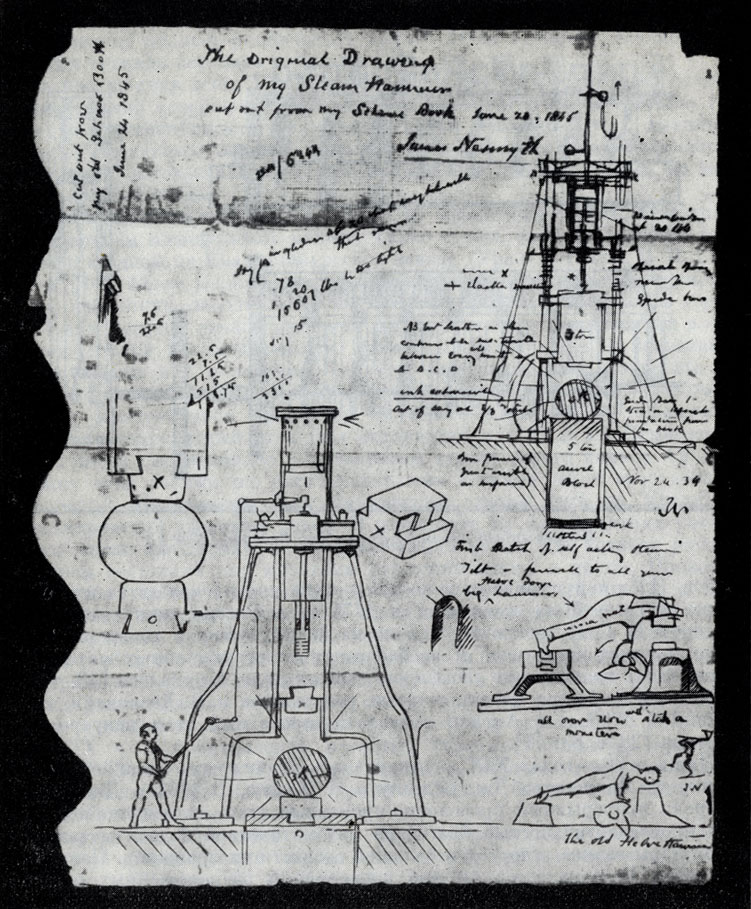
Паровой молот Дж. Несмита. Рисунок автора (патент 1839 г.)
В 1841 г. паровой молот системы Несмита был построен во Франции и применен на заводах акционерного общества «Шнейдер и К°» в Крёзо [48, с. 30]. В 1842 г. Дж. Несмит создал паровой молот на своем заводе в Манчестере. С этих пор паровые молоты стали быстро внедряться на предприятиях многих стран мира, причем в промышленности наряду с молотами двойного действия применяли и молоты простого действия, как правило, большой мощности для отковки особо крупных поковок и деталей машин.
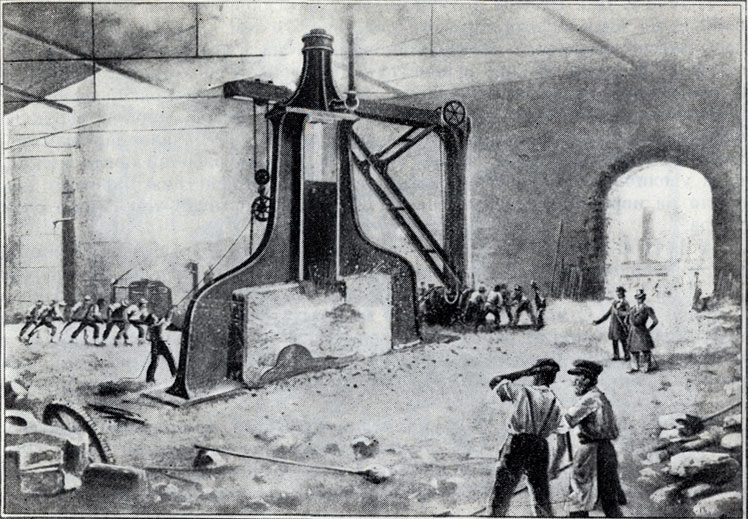
Паровой молот Дж. Несмита в действии
Рассматривая становление капиталистического машинного производства, К. Маркс в «Капитале» обращает внимание на паровой молот Несмита как на один из ярких примеров технического прогресса в области машиностроения, вызванного промышленной революцией конца XVIII - начала XIX в.
К. Маркс отмечал: «...один из таких паровых молотов, которые являются изобретением Несмита, весит более 6 тонн и падает перпендикулярно с высоты 7 футов на наковальню весом в 36 тонн. Он легко превращает в порошок гранитную глыбу и не менее способен к тому, чтобы вбить гвоздь в мягкое дерево рядом легких ударов» ().
В 70-х годах XIX в. в промышленности использовали паровые молоты с весом падающих частей от 50-100 т и более. Так, на заводе Крупна в Эссене (Германия) был изготовлен 75-тонный паровой молот [49]. В 1873 г. на Всемирной выставке в Вене экспонировалась модель установленного на Пермском пушечном заводе 50-тонного молота - самого мощного в то время в мире парового молота двойного действия. В Европе наиболее мощный тогда 35-тонный паровой молот двойного действия находился в Вульвичском арсенале (Англия).
Крупный вклад в теорию & практику конструирования кузнечного оборудования внес русский ученый И. А. Тиме. В 1867 г. по его проекту на Луганском заводе был построен один из первых в России молотов простого действия [48, с. 30; 50].
Мощный 120-тонный паровой молот был установлен в 1877 г. во Франции на заводе акционерного общества «Шнейдер и К°» в Крёзо [51, с. 19].
Однако развитие крупных паровых молотов выявило ряд их недостатков, заставивших инженеров и конструкторов работать над созданием кузнечных машин нового типа - гидравлических прессов. Недостатки паровых молотов проявились прежде всего в сильных ударах, сотрясающих почву в окрестностях цехов и заводов, что стало опасным для окружающих построек и сооружений. Кроме того, эти сотрясения могли разрушить сами молоты, эксплуатация которых была весьма сложна и дорога.
Прессы оказались свободными от указанных недостатков, в результате чего они быстро вытеснили паровые молоты, особенно большой мощности.
Начало развития гидравлических прессов связано с именем английского инженера-механика Дж. Брамы. В 1797 г. он выдвинул идею создания гидравлического пресса для прессования свинцовых труб путем продавливания металла через кольцевое отверстие матрицы. В 1820 г. Т. Бурр построил первый практически пригодный гидравлический пресс [28, с. 627-628].
С созданием гидравлических прессов наметились два основных направления их использования: в технологии прессования (выдавливания) металла через отверстие матрицы и в ковочно-штамповочных производствах (ковка, объемная и листковая штамповка). К 60-м годам XIX в. относится применение первых гидравлических прессов для волочения крупногабаритных труб и профилей, для испытаний материалов и др.
Попытки применить гидравлические прессы в ковочно-штамповочных производствах относятся к началу 50-х годов XIX в. В 1851 г. на Лондонской всемирной выставке экспонировался 4-цилиндровый пресс, который давал давление 2500 т. Он предназначался для штамповки небольших предметов малой толщины. В 1859-1861 гг. Дж. Газвелл построил и установил в железнодорожных мастерских Вены свой первый пресс для штамповки паровозных деталей: поршней, крейцкопф, рессор, хомутов, кривошипов и др. Рабочий цилиндр этого пресса получал воду под давлением 400 ат. Первые прессы, построенные Дж, Газвеллом, имели мощность 700, 1000 и 1200 т. Один из этих прессов экспонировался в 1862 г. на Всемирной выставке в Лондоне [51, с. 22].
Пресс Газвелла, давая большие возможности для производства паровозных и других крупных деталей, однако, не был приспособлен для обработки литых слитков. Первую попытку применить гидравлический пресс для ковки слитков предпринял в 1861 г. Гледхилл (Англия), но промышленное использование началось с работ английского инженера Дж. Витворта, который в 1884 г. в Манчестере успешно применил пресс для ковки стали, изготовляя из слитков стволы орудий. Насколько прогрессивным оказался способ прессования, показывают следующие данные. На одном из шеффильдских заводов в Англии для расковки слитка весом 36,5 т, предназначенного для ствола орудия, под 50-тонным молотом требовалось 3 недели и 33 промежуточных нагрева, в то время как слиток весом в 37,5 т под 4000-тонным прессом обрабатывался всего за 4 дня, для чего требовалось 15 нагревов [51, с. 24]. Широкое распространение гидравлических прессов в производстве относится к 80-90-м годам XIX в. и затрагивает хронологические рамки, выходящие за пределы рассматриваемого периода. Подчеркнем лишь, что гидравлические прессы, потеснившие большие и частично средние паровые молоты, в результате специфики технологии продолжали широко применяться для горячей штамповки.
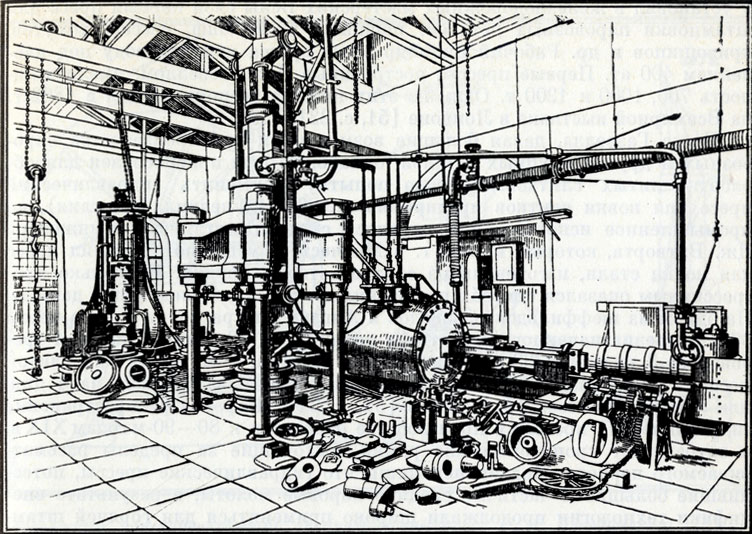
Гидравлический пресс Дж. Газвелла (вторая половина XIX в.)
Развитие паровой энергетики и машиностроения существенно повлияло на технику чеканки, широко распространенную в металлообрабатывающих производствах, монетных дворах, а также в ювелирно-художественных ремеслах. Техника чеканки, особенно на монетных дворах, так же как и применявшиеся в их производствах станки, всегда привлекали к себе внимание лучших мастеров-изобретателей, инженеров и ученых. Это объясняется, во-первых, спецификой монетного производства, в котором большой удельный вес в качестве исходных материалов составляли благородные металлы (золото и серебро), выполнявшие функции валютных металлов, и, во-вторых, сложностью самого технологического процесса, предъявлявшего высокие требования к получению необходимых металлов и сплавов, их механической обработке, особенно к чеканке [52; 53]. Чеканка - один из главных и завершающих процессов монетного производства, отличающийся большой трудоемкостью и высокими требованиями к точности работы чеканных прессов и стойкости инструмента (штемпелей).
Вот почему изобретательская мысль мастеров и инженеров непрерывно работала над усовершенствованием чеканной техники Не случайно ранние образцы винтовых чеканных прессов, применявшихся на монетных дворах в XVII - начале XVIII в., обычно изготовляли цельнометаллическими - из чугуна или бронзы, в то время как при конструировании большинства других станков широко использовали дерево и лишь отдельные ведущие их элементы были металлическими [54].
Первые чеканные прессы приводились в движение вручную. Верхний штемпель нажимал на монетный кружок с помощью винта, соединенного с «воротягой», на концы которой для усиления действия надевали массивные «груши». Монетные кружки подкладывали под штемпели и снимали вручную.
В 1786 г. в технике чеканки произошли серьезные изменения, вызванные изобретением усовершенствованного монетопечатающего пресса системы П. Дро. Пресс был снабжен автоматическим приспособлением для подачи кружков и сбрасывания готовых монет [55, с. 11], для чего служил специальный механизм, использующий силу отдачи винта при ударе. Кроме того, в станке было предусмотрено разъемное кольцо, которое с печатанием рельефа автоматически обжимало монетный кружок, нанося насечку или отпечатывая буквы на кромке монеты. Важной заслугой Дро является перевод технологии чеканки с ручного на механический привод. Для этого изобретатель использовал принцип откачивающего насоса Ньюкомена, решив проблему пневматической передачи с помощью «воздушного снаряда» - насоса простого действия, приводящего в движение несколько поршней, соединенных с соответствующими рабочими органами прессов.
Механические чеканные прессы системы П. Дро с пароатмосферной машиной Ньюкомена распространились на монетных дворах многих стран. В 1808 г. Д. Уатт и М. Болтон применили на Лондонском Монетном дворе для привода чеканных прессов универсальную паровую машину [56].
Однако принципиально по-новому к технике чеканки подошел русский изобретатель И. А. Неведомский, создавший в 1810-1811 гг. на Петербургском Монетном дворе первый в мире рычажный монетопечатающий автоматический станок, общая конструкция и принцип действия которого легли в основу современных чеканных машин. В коллекциях Отдела нумизматики Эрмитажа (Ленинград) хранятся два медных жетона, отчеканенных на изобретенном И. А. Неведомским рычажном прессе, усовершенствованном им в 1812-1813 гг. Оба жетона посвящены изобретению И. А. Неведомского и имеют отчеканенные надписи; на первом выбито: «Росс, изобретение. Спб. И. Н.», на втором - «Русское изобретение. И. Н.» [55, с. 5]. Однако изобретение, которое И. А. Неведомский подробно описал в своей книге [57], не оценили по достоинству в России. Вместе с тем оно было встречено с большим интересом как крупное техническое новшество за границей. Производство станков системы И. А. Неведомского организовала немецкая фирма Д. Ульгорна, а сами станки под названием «ульгорповских», вскоре получили всеобщее распространение. Первая машина была установлена в Дюссельдорфе уже в 1818 г., в 1820 г. их применили на Берлинском Монетном дворе; в 1870 г. построенные заводом Ульгорна машины работали на 38 монетных дворах мира, в том числе и в Петербурге (с 1840 г.) [55, с. 24; 58].
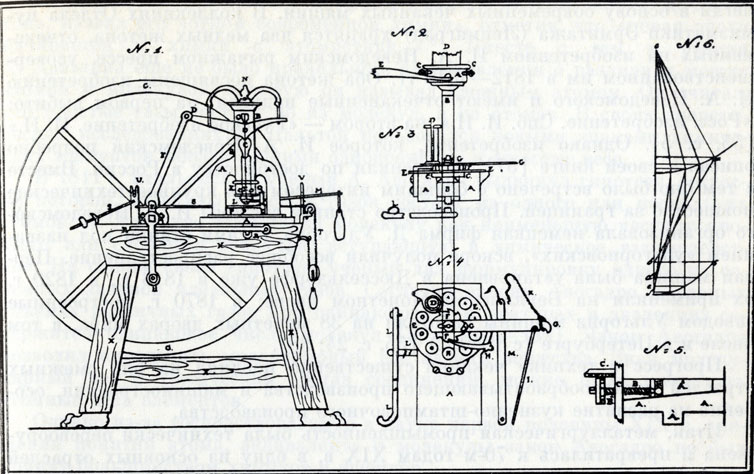
Рычажный монетопечатающий автоматический пресс И. А. Неведомского (1811 г.) и его основные узлы. Чертеж из книги И. А. Неведомского
Прогресс в технике чеканки существенно повлиял на ряд смежных отраслей металлообрабатывающего производства и машиностроения, особенно на развитие кузнечно-штамповочного производства.
Итак, металлургическая промышленность была технически перевооружена и превратилась к 70-м годам XIX в. в одну пз основных отраслей крупной капиталистической индустрии. Мировая выплавка чугуна увеличилась с 278 тыс. т в 1790 г. до 12 млн. т в 1870 г.